Inzicht, samenwerking en doorzettingsvermogen brengen onderzoekscentrum imec dicht bij een doorbraak in hoe toekomstige mobiele OLED-schermpjes gemaakt kunnen worden.
De schermpjes van onze mobiele telefoons worden steeds complexer. Ze bedekken zo veel mogelijk van het oppervlak, waardoor er geen randjes overblijven voor zaken als de cameralens, licht- en vingerafdruksensor. Deze zullen zich in toenemende mate achter het scherm moeten gaan bevinden. Niet eenvoudig, want dat wil zeggen dat het scherm licht van buiten moet doorlaten tot bij de camera en sensoren, maar tegelijk een helder beeld met hoog contrast moet uitstralen.
Ook de resolutie van OLED-schermen blijft een belangrijke uitdaging. Niet alleen voor smartphones, maar met name ook voor ontluikende toepassingen zoals holografie en augmented en virtual reality (AR/VR). Imec-onderzoekers Tung-Huei Ke en Pawel Malinowski verklaren: “Momenteel zijn resoluties mogelijk tot 3000 pixels per inch (ppi) met behulp van witte OLEDs en kleurfilters. Voor de volgende generaties displays heeft de industrie behoefte aan een verdubbeling tot 6000ppi. Om dit mogelijk te maken, zijn pixels nodig met afmetingen van een micrometer, ofwel een grootteorde lager dan wat momenteel gangbaar is.”
Nood aan een nieuwe productietechniek
Om OLED-displays te maken, gebruikt de industrie technieken zoals inkjet printing of selectief opdampen van materialen met behulp van maskers. Deze bestaande technieken lopen om allerlei redenen tegen hun grenzen aan. Maar vanuit onverwachte hoek lijkt nu een beloftevol alternatief zo goed als klaar voor overdracht naar de industrie: fotolithografie.
Tung-Huei Ke: “Lithografie is een veelgebruikte techniek bij de productie van computerchips. Ze laat toe om elektronische structuren op nanometerschaal te realiseren. Maar niemand hield het voor mogelijk om het in te zetten voor OLEDs. Deze zijn namelijk heel gevoelig voor parameters als temperatuur en vocht en daardoor zouden de OLEDs stukgaan tijdens het lithografieproces . De pogingen om het toch te proberen strandden dan ook vrij snel.”
Waarom is het imec dan wel gelukt? Kort samengevat: het inzicht en doorzettingsvermogen van een kleine groep onderzoekers met domeinoverschrijdende expertise, een manager en context die de experimentele cultuur stimuleerden en af en toe een duwtje in de rug van de nodige samenwerkingspartners.
Hoe imec op het idee van lithografie kwam
Tung-Huei Ke: “Tien jaar geleden werkten we aan het patroneren van organische materialen voor nieuwe soorten zonnecellen. In onze zoektocht naar de juiste lichtgevoelige materialen (fotoresist) vonden we in Fujifilm een betrokken partner. Zij stuurden ons samples en een van hun experts, Nakamura-san, met wie we doorheen al die jaren fantastisch hebben samengewerkt, kwam als industriële resident met ons aan het project werken. Met een bescheiden R&D budget begonnen we de eerste experimenten en na een vijftiental samples kwamen we op de eerste beloftevolle resultaten.”
Pawel Malinowski: “Op dat moment kwamen de interdisciplinaire inzichten om de hoek. Onze groepsleider Paul Heremans opperde het idee om - als het voor organische zonnecellen werkte - lithografie ook voor de meer uitdagende organische LEDs te proberen. En met Tung Huei beschikte ons team over een van de weinige onderzoekers ter wereld die zowel iets afwist van lithografie als van OLED-schermen. Je moet weten dat in die periode OLED nog heel exotisch was. Nu is het een gangbare term in consumentenproducten en worden er televisies mee gemaakt, maar toen was het zelfs in de onderzoekswereld nog maar de vraag of er überhaupt ooit een grote afzetmarkt voor zou zijn.”
Vijf jaar om te bewijzen dat het kan
De initiële inzichten leidden in 2013 tot het allereerste persbericht over lichtgevoelige materialen voor de toepassing van lithografie bij de productie van OLEDs. Wat volgde was een aantal jaren van intensief laboratoriumwerk. Pawel Malinowski: “Die eerste jaren waren een geweldige tijd waarin we ons als onderzoekers konden uitleven. Als klein team vulden, en voelden, we elkaar ook perfect aan.”
Tung-Huei Ke: “Het was echt stapje voor stapje en elk succes vierden we samen. Zo ben je in het begin al blij dat je überhaupt een OLED-pixel kan maken die licht geeft. Toen het ons in 2013 voor de eerste keer lukte, stonden we er dan ook met z’n allen naar te kijken zoals kleuters naar de lichtjes van de kerstboom. En dat voor de volle twee minuten, want een langere levensduur was onze eerste OLED-pixel niet beschoren (lacht).”
Van die ene pixel ging het een jaar later naar twee kleuren en weer een jaar later naar drie (RGB: rood, groen, blauw). Tung-Huei Ke: “Door het zo samen te vatten lijkt het alsof het een eenvoudige opschaling was van een naar drie pixels, maar op de achtergrond ging het gepaard met een heel aantal aanpassingen aan de materialen en processen.” Pawel Malinowski: “Er was ook zo goed als geen wetenschappelijke literatuur waar we op konden bouwen, dus we moesten zowat alles zelf uitproberen. Gelukkig heb je bij organische chemie altijd veel materialen om uit te kiezen, dus als je op een probleem stoot, kan je altijd wel een oplossing vinden. Alleen heb je ook veel opties die je moet uitproberen, dus dat maakt het dan weer niet eenvoudig.”
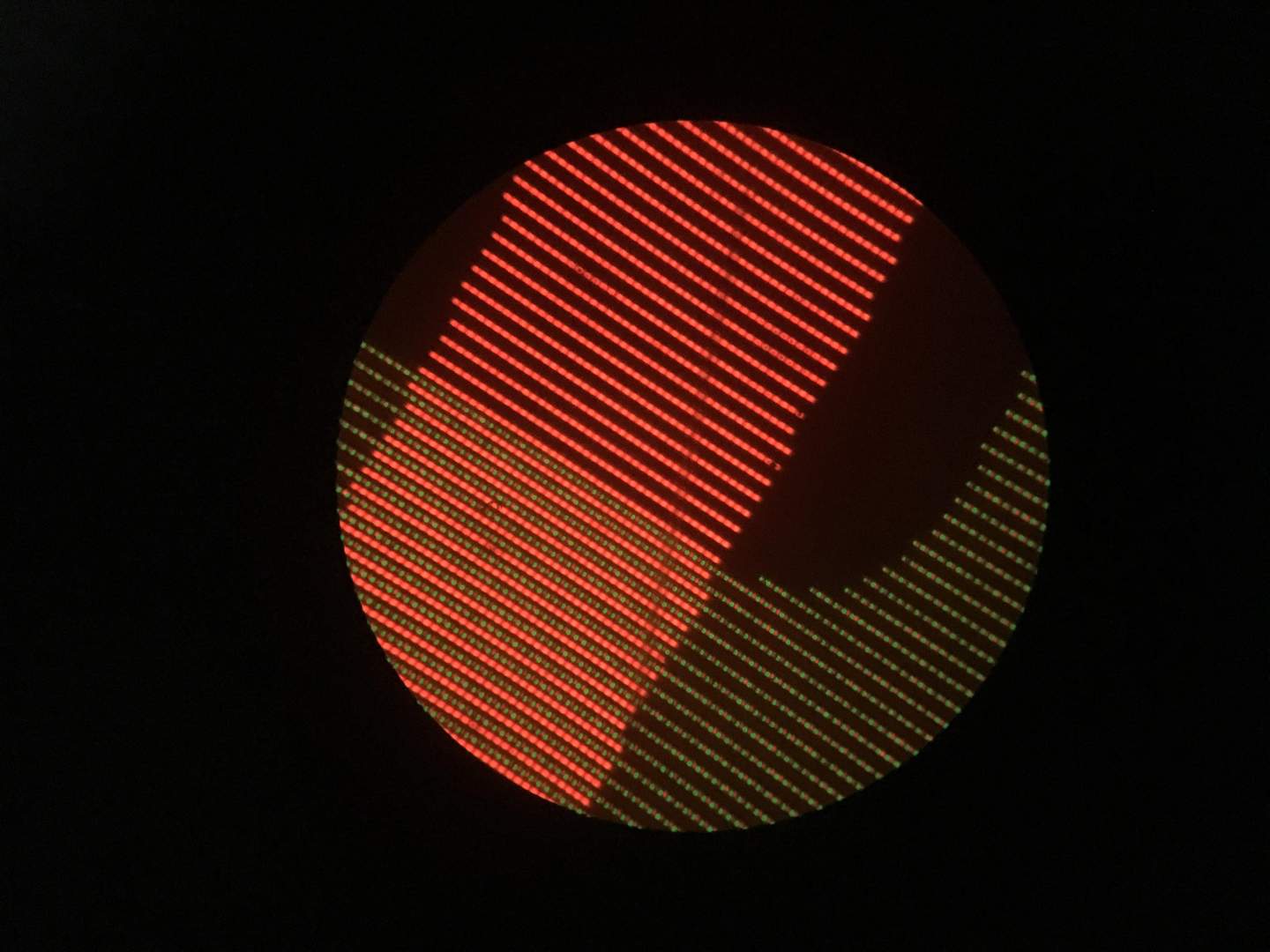
Toen het bewezen was dat imec met lithografie een RGB-pixelcombinatie kon maken, verschoof de focus in het onderzoek ook naar andere aspecten, zoals het verlengen van de levensduur. Dat was in 2015-2016, het moment waarop het team ook begon te praten met display-producenten.
Optimalisatie dankzij samenwerkingen met de industrie
Pawel Malinowski: “Kort na de aankondiging van onze RGB-pixels organiseerden we een zakenreis doorheen Azië om raakvlakken te zoeken met de display-industrie. We hebben toen in drie weken tijd zoveel landen en steden bezocht dat ik op de duur zelfs niet meer wist in welke stad ik was. Maar het leverde een hele reeks boeiende gesprekken op en aan het eind ook een aantal concrete samenwerkingsprojecten.”
De opgedane inzichten en samenwerkingen met de industrie hielpen om het onderzoek gerichter te voeren in functie van de behoeften van de display producenten. Zo publiceerde het team in 2017 toonaangevende resultaten op het vlak van kleine pixelafmetingen en afstand tussen pixels. Ook verbeterde de levensduur van onze OLED-displays aanzienlijk in vergelijking met de oorspronkelijke twee minuten.
Pawel Malinowski: “Na zowat dertig pogingen hadden we een display sample met een levensduur waarin we vertrouwen hadden. Toch zal ik onze eerste conferentie waarop we deze toonden nooit vergeten. Op Touch Taiwan, een toonaangevende display-conferentie, had onze industriële partner CPT aangeboden om onze display-sample te tonen op hun beursstand. Dat was een hele eer omdat daar enkel de beste resultaten worden getoond en ook de reputatie van het bedrijf eraan vasthangt. In de beurshal was het zowat vijftig graden Celsius met een luchtvochtigheid van bijna honderd procent: niet meteen omstandigheden waar OLEDs blij van worden. Daarenboven bleek dat de mensen die de beursstand aan het opbouwen waren onze sample hadden meegenomen in een vuile draagtas onder hun bezwete arm. Het was de dag voor de grote VIP-opening, dus je kan je inbeelden dat ik die nacht niet veel geslapen heb (lacht). Maar onze sample deed het perfect en zelfs tot op vandaag hebben we hem bewaard en doet hij het nog. Een beter bewijs van levensduur konden we ons niet inbeelden.”
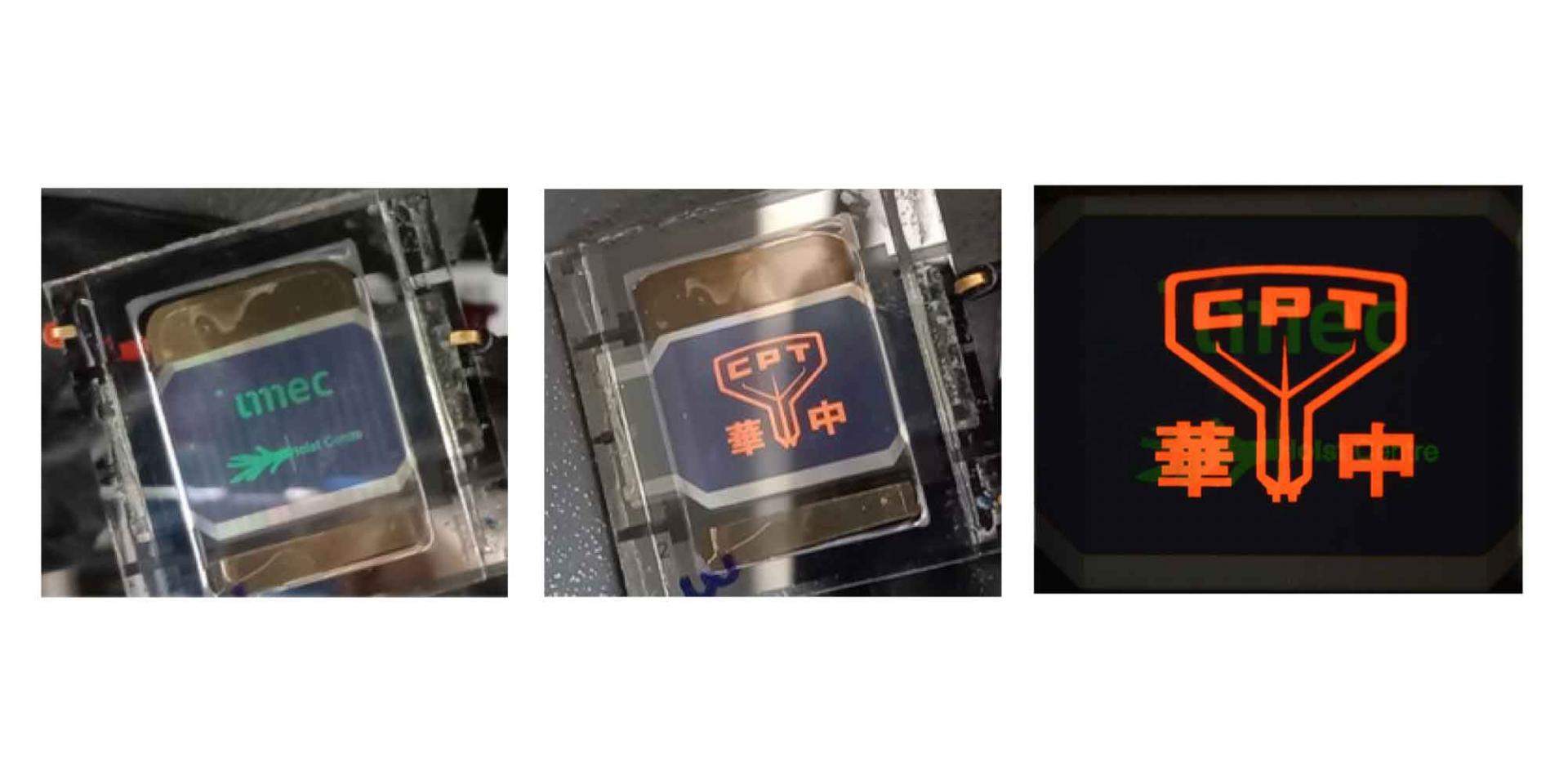
Tung-Huei Ke: “De reden dat we op dit punt geraakt waren, is omdat we rigoureus alle defecten en hun mogelijke oorzaken hebben onderzocht en aangepakt. Een OLED-display kan uit een tiental lagen bestaan. In elk van deze lagen, en op elk van hun overgangen, kan een defect ontstaan. Een van de sterktes van imec is dat het een wereldwijd unieke expertise en infrastructuur heeft om alle gangbare testen uit te voeren naar de levensduur, betrouwbaarheid en defecten van elektronische circuits. De mogelijkheid om over de hele breedte analyses uit te voeren was noodzakelijk om dit traject succesvol te kunnen doorlopen. En het verklaart ook mee waarom we bij imec als eerste en enige in de wereld geslaagd zijn in een opzet dat niemand voor mogelijk achtte: OLED-pixels maken met behulp van lithografie.”
De eerste transparante vingerafdruksensor
Pawel Malinowski: “Hoe meer we met de industrie gingen samenwerken, hoe ‘serieuzer’ ons werk ook werd. De opdrachten en deadlines van partners zorgden voor meer stress dan in onze zorgeloze beginjaren, maar tegelijk ook voor concrete doelen die de voortgang versnelden. Tegelijk bleef het ook belangrijk om te experimenteren. We halen nog steeds veel voldoening uit zijprojecten die we zoveel mogelijk proberen op te starten.”
Zo opperde Pawel Malinowski rond 2018 om een organische lichtsensor (OPD, organische fotodiode) te maken naast een OLED-pixel. Dit zou toelaten om sensoren voor bijvoorbeeld vingerafdrukken te integreren in de mobiele display. Maar daarvoor moeten de lagen er bovenop wel transparant zijn om invallend licht tot bij de sensor te krijgen. In de praktijk betekent dit dat er ‘gaatjes’ moeten gemaakt worden tussen reeds werkende OLED-pixels zonder dat deze beschadigd raken. Ook hiervoor zette imec met succes lithografietechnieken in. Zo won het team op de SID Display Week in 2019 de prijs voor beste prototype met een transparante vingerafdruksensor.
Van het lab naar productie: de ultieme test
Als meest recente resultaten presenteerde imec eind 2020 dankzij lithografie twee doorbraken die ontzettend belangrijk zijn met het oog op industriële productie: de creatie van pixels met een afmeting van 10 micrometer en een tussenafstand van 20 micrometer, en de creatie van ‘gaatjes’ in het display, voor ingebouwde sensoren. Beide zonder noemenswaardig effect op de lichtgevende eigenschappen van de OLEDs.
Voor de overdracht naar de industriële productie van geavanceerde mobiele displays moeten wel nog enkele hordes worden genomen. Met als belangrijkste het terugbrengen van het stroomverbruik. Als enige nadelig effect na het lithografieproces zien de onderzoekers namelijk dat het stroomverbruik van de OLED-pixels toeneemt. Dit zou een te hoog batterijverbruik met zich meebrengen voor mobiele toestellen.
Tung-Huei Ke: “Momenteel zien we een verbruik van 6,6V, wat hoger ligt dan de 3,8V waar we minimaal naartoe moeten. Wel zien we dat een herhaling van meerdere lithografiestappen geen cumulatief effect heeft. Dit geeft ons een indicatie dat het probleem zich stelt in de eerste stappen van de productie. Ik ben overtuigd dat we met dit inzicht binnen afzienbare tijd de precieze oorzaak en bijhorende oplossing zullen vinden.”
Wat afzienbare tijd betekent valt moeilijk te voorspellen. Pawel Malinowski: “Onze experimenten duren typisch een aantal weken en dat kan soms voor onverwachte problemen en de nodige frustraties zorgen. Als er bijvoorbeeld een stroomonderbreking is in het lab waarin onze experimenten lopen, kan het zijn dat we dat experiment helemaal opnieuw moeten opstarten. Maar we kunnen ook veel voortgang boeken als de industrie haar actieve deelname aan het onderzoek nog verder opkrikt.”
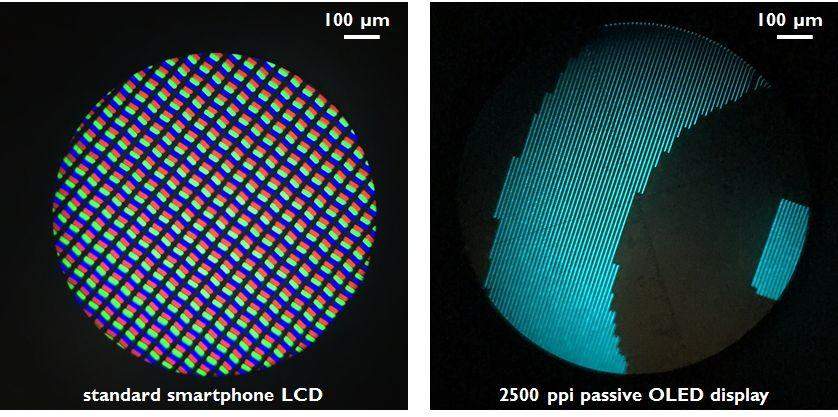
Tung Huei Ke: “Het belang van dit onderzoek is echt niet te onderschatten. Als de industrie wil blijven innoveren in OLED-displays voor smartphones en ook nieuwe markten wil bedienen zoals AR en VR, moet ze op zoek naar nieuwe productiemethodes. De introductie van lithografie zou hierin weleens van groot belang kunnen blijken. Ook technische opleidingen kunnen een belangrijke bijdrage leveren. In Azië studeren ingenieurs af met al een zekere kennis van organische elektronica. In België blijven de opleidingen helaas vooralsnog beperkt tot de meer basisaspecten van elektronica, waardoor we pas afgestudeerden uit Europa vaak nog heel erg moeten coachen en inwerken voor ze een actieve bijdrage kunnen leveren aan ons onderzoek. Bij imec hebben we samen met enkele industriële partners meer dan tien jaar geïnvesteerd om de haalbaarheid van de technologie te bewijzen. Ik ben ervan overtuigd dat we in polepositie liggen om bedrijven te helpen om deze technologie nu ook effectief naar de markt te brengen.”