Dankzij biologische en chemische processen produceren we vandaag een uitgebreid assortiment eindproducten - van cosmetica en wasmiddelen tot essentiële voedingsingrediënten en levensreddende farmaceutica. Wat als deze productieprocessen niet alleen efficiënter worden, maar ook slimmer?
Uitdagingen in procesanalyse
Om de efficiëntie van biologische- en chemische productieprocessen te verbeteren, is nauwkeurige kwaliteits- en procesbeheersing essentieel. Het verzamelen van de juiste data en kennis is daarbij cruciaal.
Neem de uitdagingen in biomanufacturing, zoals bijvoorbeeld bij de biologische productie van menselijke cellen in het kader van stamcel- of CAR-T-therapie: een tijdskritiek proces waarbij het eindproduct zeer gevoelig is voor de geringste procesvariatie. Traditionele procesbeheersing omvat daarom vaak 'offline' monitoring, waarbij monsters uit de procesflow worden genomen voor verdere analyse. Zulke metingen geven een indicatie over de kwaliteit van het huidige product en leveren heel wat interessante inzichten voor volgende producties, maar laten – ondanks de kost en tijdsinvestering – niet toe om het huidige proces bij te sturen. Deze innovatieve therapieën betaalbaar en kwalitatief op de markt brengen, blijft dan ook een hele uitdaging.
Een idealer scenario is het 'inline' monitoren van een productieproces, waarbij de onderliggende mechanismen in real time worden gemeten én bijgestuurd – mogelijk zelfs automatisch. Dit zou niet alleen de totale productietijd verkorten en kosten kunnen reduceren, maar ook verbruik van grondstoffen en energie verminderen en zelfs de kwaliteit van het eindproduct verbeteren. Hoewel dergelijke inline sensoren bestaan, blijven ze verre van de standaard.
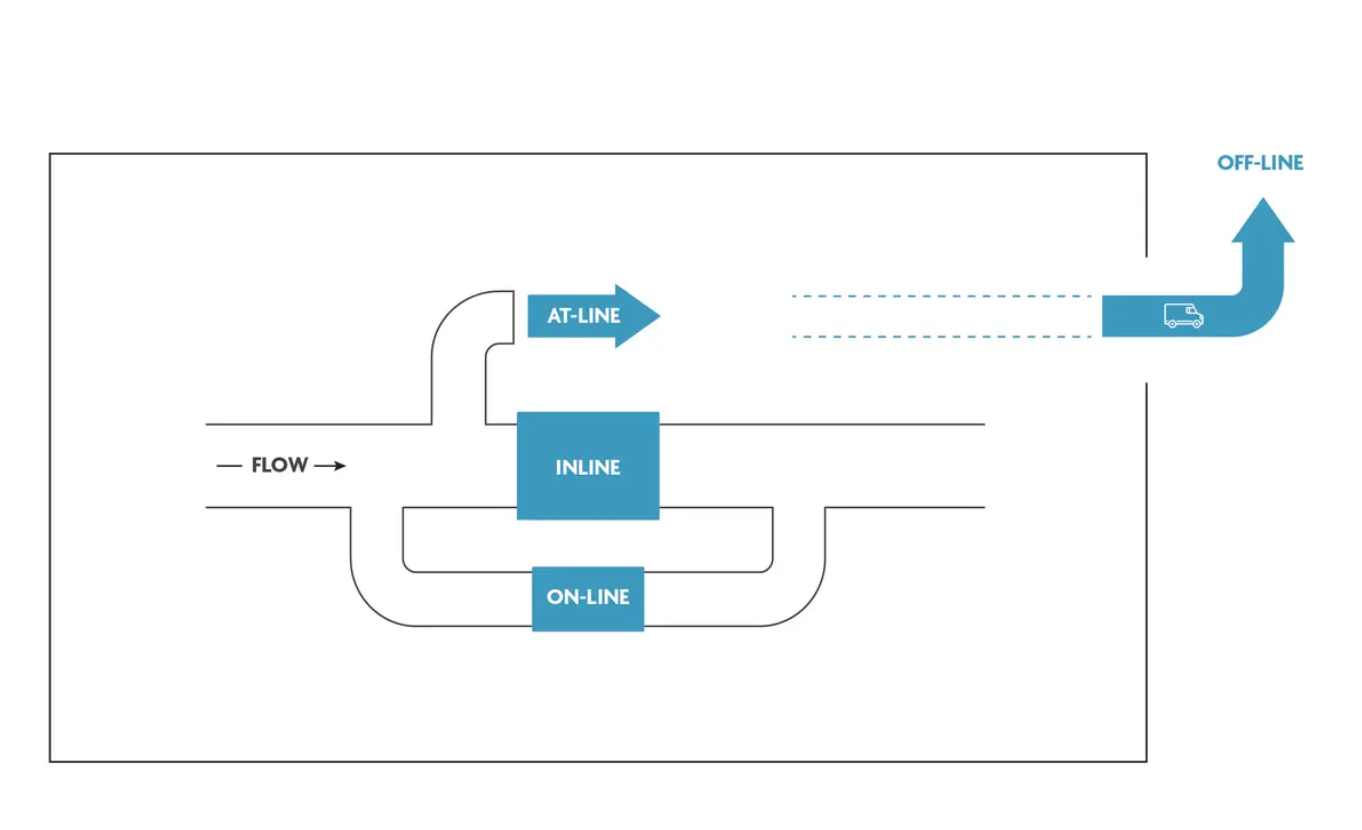
Inline monitoring met chiptechnologie
"Probes voor inline monitoring, zoals die voor pH- en temperatuurmetingen in een bioreactor, bestaan al meer dan 40 jaar. Maar om alle relevante parameters te meten heb je al snel een hele hoop probes en offlinesystemen nodig, wat problemen geeft in installatie, kalibratie, dataverwerking en zelfs sterilisatie. Dankzij imecs expertise in chiptechnologie, zijn we er in geslaagd om verschillende inline sensoren te miniaturiseren en combineren in één probe, waardoor deze problemen verdwijnen.” aldus Bert Verbruggen, programma-manager bij imec. “Verder bouwend op onze eerdere ontwikkelingen in geminiaturiseerde sensoren, zijn we er op amper anderhalf jaar tijd in geslaagd om van een probleem naar een commercieel betekenisvolle oplossing te gaan.”
Concreet hebben de imec-onderzoekers een procesanalysetechnologie (PAT) sensor ontwikkeld in de vorm van een probe. Deze geïntegreerde, geminiaturiseerde, en multi-parametrische sensor kan essentiële parameters zoals temperatuur, opgeloste zuurstof, elektrische conductiviteit, glucose, lactaat en zelfs de densiteit van de cellen tegelijkertijd in real time meten, bijvoorbeeld in een bioreactor. Eenmaal getoetst aan het protocol en eerdere kennis, bieden deze kritieke procesparameters (KPP) een indicatie van de kwaliteit van het eindproduct.
In een volgende stap willen de onderzoekers de tijdspanne van metingen verlengen (nu: twee weken), en een closed-loop systeem ontwikkelen waarin productieprocessen automatisch worden bijgestuurd op basis van tussentijdse metingen. Naast zijn pioniersrol in nanotechnologie ondersteunt imec op deze manier Vlaanderen in het verstrekken van technologische oplossingen om zijn voorsprong in de farmaceutische industrie te behouden.

De rol van AI in het begrijpen van de procescomplexiteit
Door het inzetten van dergelijke sensoren kunnen aanzienlijke hoeveelheden meetgegevens worden verzameld. Dat is nodig, want (bio)chemische processen zijn zeer complex, wat hun voorspelbaarheid bemoeilijkt. Er is dan ook nood aan de ontwikkeling van geavanceerde modellen, om inline metingen naadloos te integreren met historische data en specifieke patronen. Ondersteund door kunstmatige intelligentie (AI), kunnen we gedetailleerde voorspellingen ontwikkelen omtrent kritieke kwaliteitskenmerken (KKK), zoals het percentage correct gevouwen proteïnen in farmaceutica. Dat soort parameters is vaak moeilijk direct meetbaar, maar dankzij AI met een grote graad van zekerheid voorspelbaar. Met die inzichten kunnen productiesites aan de slag om tijdig in het proces in te grijpen, de kwaliteit te verzekeren en onnodige kosten en tijdverlies te vermijden.
Die aanpak werd getest tijdens het Catalisti DAP2CHEM project. Antwerpse onderzoekers van IDLab, een imec-onderzoeksgroep aan UAntwerpen en de UGent, bouwden een digitaal simulatieplatform van een ‘Chemical Development Pilot Plant’ (of ook: een proeffabriek), in samenwerking met Johnson & Johnson en de KU Leuven. Een bescheiden dataset van procesmetingen werd hiervoor samengevoegd met specifieke domeinkennis (chemische procesinformatie, zoals het verloop van de reacties) tot een hybride simulatiemodel en een optimalisatiemodel op basis van ‘deep reinforcement learning’.
Hiermee konden duizenden virtuele experimenten uitgevoerd worden (of ook: in silico-onderzoek) – aantallen waarvan je op fabrieksniveau enkel kan dromen. Het resultaat: een geoptimaliseerd recept dat de hoeveelheid benodigde solvent, tijd en kosten tot wel 30% verminderde. Bovendien leidde deze aanpak tot minder afvalproductie, een zuiverder eindproduct, en een energiebesparing tot wel 10%.
Siegfried Mercelis van IDLab Antwerpen: “In dit project hebben we kunnen aantonen dat innovaties op basis van AI zich niet hoeven te beperken tot theoretische concepten, maar zelfs met een beperkte hoeveelheid data veel waarde kunnen creëren. Naarmate geavanceerdere sensoren worden geïntegreerd in de procesflow (zoals de PAT probe), neemt de behoefte aan complexe en tijdrovende modellering verder af en wordt de schaalbaarheid van de AI-gestuurde technologie verder vergroot. De unieke combinatie van imecs expertise op zowel hardware- als AI-gebied schept dus mogelijkheden voor aanzienlijke optimalisaties in processen, variërend van biomanufacturing tot voedselproductie.”
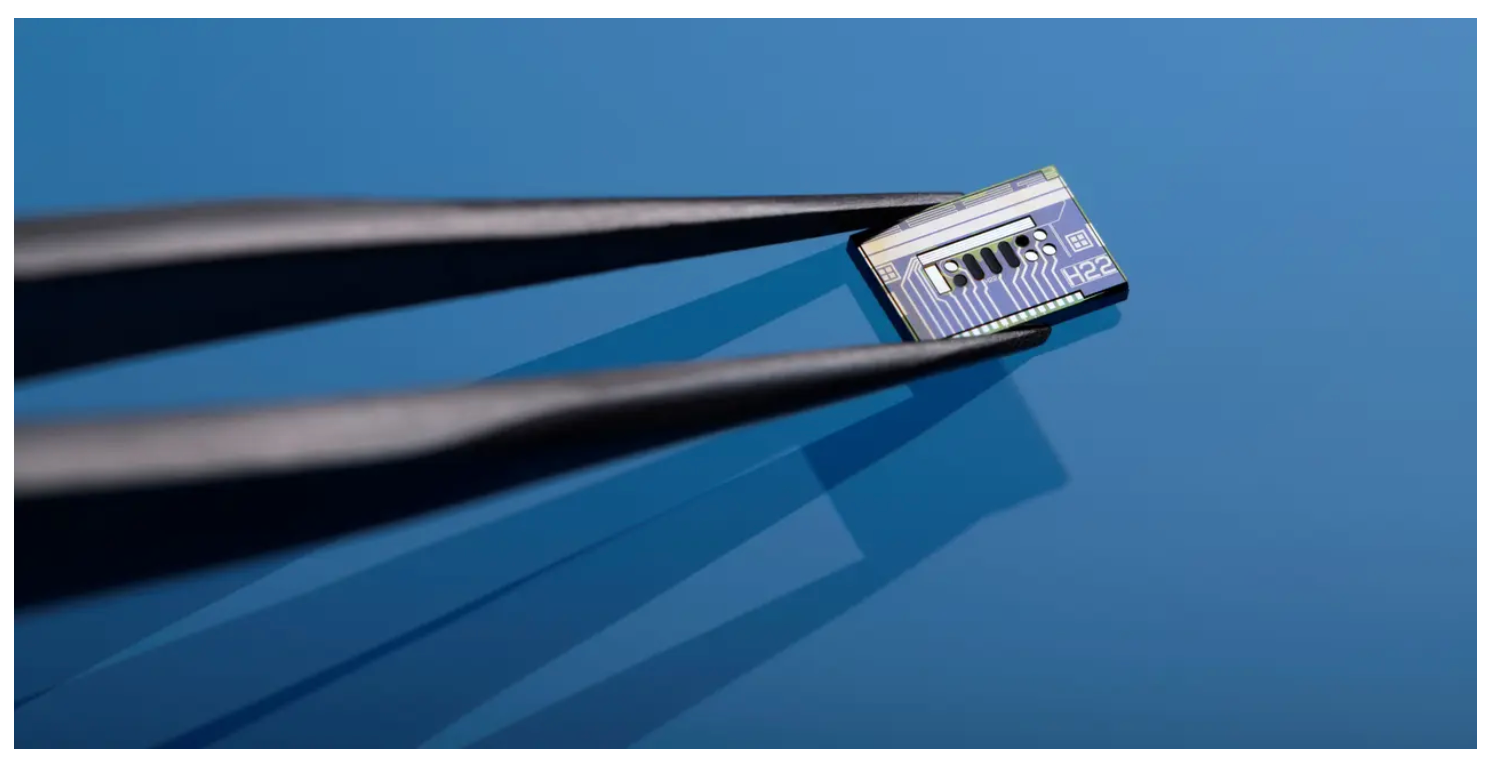
Van mysterieus model naar leermeester
Ondanks de onmiskenbare voordelen van AI blijft de implementatie ervan in de industrie voorlopig echter beperkt, deels vanwege het 'black-box' karakter ervan. De imec-onderzoekers in DAP2CHEM gingen daarom nog een stap verder en ontwikkelden een transparant ‘explainable’ AI-gestuurd model (XAI) dat verstaanbaar, met behulp van een interface en in mensentaal, uitlegt hoe besluitvormingsprocessen plaatsvinden. Zo wordt het vertrouwen in de technologie door menselijke operatoren – en zelfs de interactie ermee – vergemakkelijkt. Het optimalisatiemodel is namelijk niet alleen in staat nieuwe recepten te vinden, maar kan processen ook in real time controleren en optimaliseren. Zo kan er optimaal gebruik worden gemaakt van nieuw gemeten en historische data.
Bovendien kan het AI-model, naast louter informeren, operatoren ook voor een stuk opleiden. Doorgaans is immers jarenlange ervaring nodig om cruciale processtappen te begrijpen, laat staan ze te kunnen sturen. Met de hulp van AI zou de leercurve en onafhankelijkheid van minder ervaren operatoren exponentieel kunnen stijgen.
Net daar focuste het imec.icon CHAI-project de afgelopen jaren op: een samenwerking tussen IDLab Gent en Antwerpen en een aantal industriepartners waarbinnen hybride XAI-algoritmen ontworpen worden. In twee verschillende use cases werden productieprocessen geoptimaliseerd, respectievelijk van harsen (allnex Belgium) en wasverzachters (Procter & Gamble). De implementatie begon steeds op laboratoriumschaal, waarna succesvolle resultaten werden uitgebreid naar de productieomgeving – ook hier was dit enkel mogelijk dankzij het digitaliseren van het productieproces.
Bij allnex werden bijvoorbeeld voorspellende modellen toegevoegd aan de traditionele monitoring. Deze modellen houden rekening met mogelijke scheikundige reacties, waardoor – naast het observeerbar maken van de huidige staat van het reactieproces – het model een voorspelling geeft van het eindproduct. Hierdoor weten operatoren precies wanneer ze moeten ingrijpen. Voor Procter & Gamble lag de nadruk op het beter voorspelbaar maken van de stabiliteit van nieuwe producten, zodat deze sneller op de markt gebracht kunnen worden.
Meer dan meten: met context optimaliseren
Het CHAI-consortium keerde de rollen ook om: hoe kan het AI-model leren van de expertise van operatoren – en hoe incorporeren we dit continu in ons model? Experten/operatoren werd gevraagd om sensorinfo te contextualiseren en verbanden tussen meetwaarden en productieprocessen, zoals temperatuur- of viscositeitsprocessen, aan te duiden. Deze gestructureerde benadering stelde het AI-model in staat om te leren op basis van de input en achterliggende ervaring van de kennisgever, rekening houden met zaken als anciënniteit en historische nauwkeurigheid van het individu. Dit maakt het model ook flexibel in het omgaan met ambiguïteit in meningen en leert het conflicterende feedback van operatoren op te lossen.
Michaël Rademaker van IDLab Gent, benadrukt: “We merken dat het sturen van een (bio)chemisch proces vandaag nog steeds gelimiteerd is door zowel data als kennis. Terwijl het dataluik geoptimaliseerd wordt via bijvoorbeeld de PAT- en andere sensoren, ligt de innovatie van het CHAI-project vooral in dat tweede: na identificatie van kritieke processtappen, konden we AI-gestuurde optimalisatie testen en valideren, ondersteund door menselijke expertise. Dankzij onze samenwerking met meerdere industriepartners kon er overigens op verschillende vlakken kruisbestuiving optreden, en zitten ook onze industriële partners op de eerste rij voor ontwikkelingen in procesoptimalisatie. “
Samen markeren deze projecten een paradigmaverschuiving in de (bio)chemische industrie, waarbij de synergie tussen hardware, menselijke kennis en AI leidt tot efficiëntere processen, minder afval en ongekende mogelijkheden voor innovatie. “Meten is nog steeds weten, vooral wanneer metingen worden verrijkt door expertkennis om ze in een bredere context te plaatsen. Onze projecten bewijzen dan ook dat, dankzij de kracht van hybride AI, 1 + 1 gelijk kan zijn aan 3,” besluit Rademaker.
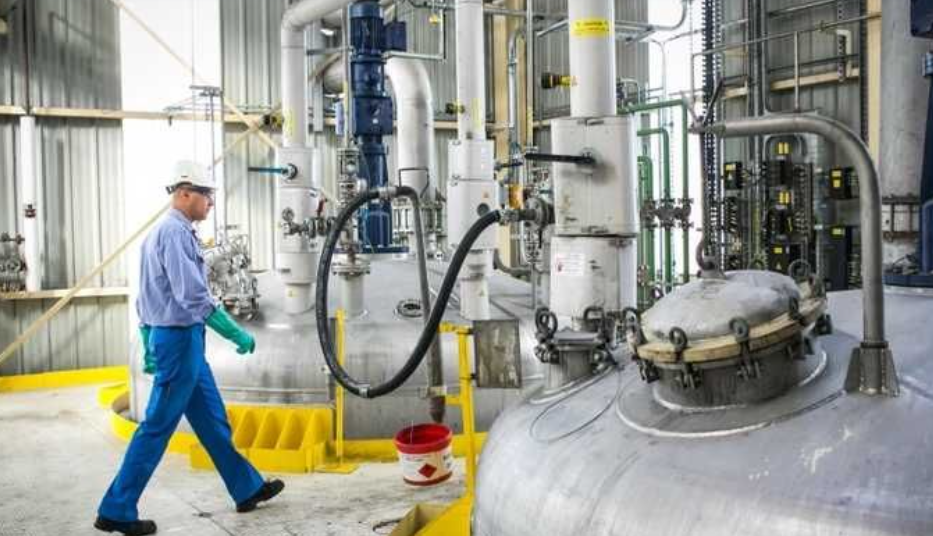
CHAI is een imec.icon-onderzoeksproject gefinancierd door imec en Agentschap Innoveren & Ondernemen (VLAIO), lopend tot maart 2024. Het CHAI-consortium bestaat uit industriepartners allnex Belgium, Dotdash, Procter & Gamble Services Company, en de onderzoekscentra IDLab Data Science Lab (UGent), IDLab IBCN (UGent) en IDLab MOSAIC (UAntwerpen).
DAP2CHEM is een innovatieproject onder de paraplu van Catalisti, de speerpuntcluster die innovatie in het bedrijfsleven in de chemische en kunststoffensector in Vlaanderen versnelt. Het project liep tot september 2022 en werd ondersteund door Flanders Innovation & Entrepreneurship (VLAIO). Het DAP2CHEM-consortium bestond uit partners imec, KU Leuven, Flanders Make, Ajinomoto OmniChem, Cronos Group, Johnson & Johnson (Janssen Belgium) en Procter & Gamble Services Company.