Wanneer elektrische auto’s massaal de weg overnemen, zal er al gauw een lawine van gedeeltelijk en compleet opgebruikte lithium-ionbatterijen ontstaan. Via reparatie, hergebruik, recycling en regulering moeten ze in het plaatje van de circulaire economie passen.
Beeld: Medewerkers van Out of Use testen afgedankte accu’s van elektrische auto’s. Bruikbare batterijen gaan naar dochter-onderneming Watt4Ever.
Dit artikel verscheen ook in de Eos special over innovatie en duurzaamheid.
Er zijn overal ter wereld initiatieven genomen om de verbrandingsmotor van de weg te duwen en te vervangen door de elektrische auto. Het Verenigd Koninkrijk heeft het voornemen om in 2030 de verkoop van conventionele auto’s volledig stop te zetten. Audi wil na 2033 alleen nog elektrische auto’s maken en de EU wil vanaf 2035 de verkoop van auto’s op benzine of diesel verbieden. Om verdere opwarming van het klimaat te voorkomen, moeten we af van transportsystemen die fossiele brandstoffen gebruiken. Elektrische auto’s hebben, wanneer ze tenminste gebruikmaken van groene stroom, een veel lagere koolstofvoetafdruk. Vandaar het motto: weg met benzine en diesel, leve de lithium-ionbatterij.
De verwachting is dat er in 2030 wereldwijd al zo’n 145 miljoen elektrische auto’s zullen rijden. Daarna zal dat aantal snel stijgen. Dat klinkt veelbelovend, maar je kan grote vraagtekens plaatsen bij de productie van lithium-ionbatterijen. Niet alleen kost het winnen van de grondstoffen – waaronder lithium, kobalt, mangaan, aluminium, koper en zeldzame aardmetalen – en het maken van de batterijen erg veel energie. Sommige materialen worden ook nog eens gewonnen met behulp van kinderarbeid of met methoden die schadelijk zijn voor mens en milieu. En dan is er nog dit: wat moet er in hemelsnaam gebeuren met de lawine van afgedankte batterijen die straks op ons afkomt?
Als er in 2030 al 145 miljoen elektrische auto’s op de weg zijn, moeten we ergens naartoe met de afgedankte batterijen
De EU wil dat tegen 2050 alle sectoren van de economie circulair zijn. Het komt erop neer dat er geen afval meer mag ontstaan. Alle grondstoffen moeten zo volledig mogelijk hergebruikt worden om milieu en klimaat te ontzien, en uiteindelijk ook om de productiekosten te drukken. Er zijn vier elementen nodig om ervoor te zorgen dat de lithium-ionbatterij een volwaardige plaats kan innemen in de circulaire economie: reparatie, hergebruik, recycling en regulering.
Reparatie
Niets is perfect. Het is altijd mogelijk dat een foutieve batterijmodule door de kwaliteitscontrole van een gigafabriek glipt, waardoor een elektrische auto al na een of twee jaar niet meer vooruit te branden is. Wat te doen? Lithium-ionbatterijen bestaan uit vijftien tot vijftig modules. Het is waarschijnlijk dat één enkele module verantwoordelijk is voor het probleem. Weggooien? Het is zowel financieel als voor het milieu veel beter die ene module te vervangen. Helaas worden de meeste lithium-ionbatterijen (nog) niet zo gefabriceerd dat ze eenvoudig te repareren zijn. Sommige producenten werken wel aan meer modulaire batterijen, die het eenvoudiger maken om een of twee modules te vervangen.
Het vervangen van zo’n module laat je beter niet over aan je handige neef die onlangs de elektrische grasmaaier repareerde. Dat zou het einde van je neef kunnen betekenen, want de batterij van een elektrische auto kan een schok van 800 tot 900 volt genereren. Garagebedrijven moeten dus over zeer goed getraind, gespecialiseerd personeel beschikken en over veilige apparatuur om zo’n batterij te openen, de foute module te identificeren en te vervangen. General Motors heeft zijn dealers in de VS laten weten dat ze elk zeker een kwart miljoen dollar moeten investeren in training en apparatuur om een rol te blijven spelen in de elektrische toekomst.
Batterijen van elektrische auto’s recyclen is technisch haalbaar, maar niet de goedkoopste optie
Dealerships en andere garagebedrijven zullen zeker gemotiveerd zijn om het repareren van lithium-ionbatterijen aan te pakken. Zo’n batterij is immers verreweg het belangrijkste onderdeel van een elektrische auto. Elektrische motoren hebben veel minder bewegende en statische onderdelen dan een benzinemotor en hebben daarom ook minder onderhoud nodig. Er zijn geen bougies om te vervangen of motorolie om te verversen.
Consultancybureau McKinsey verwacht dat de vraag naar nieuwe auto-onderdelen met 40 procent zal dalen. Wil een garage de krimpende vraag naar service compenseren, dan zal het zich op de reparatie van batterijen moeten storten. Een monteur die dat kan, zal kunnen rekenen op een zeer goed salaris.
Nowos bewijst dat reparatie van lithium-ionbatterijen lucratief kan zijn. Het Nederlandse bedrijf verzamelt en repareert de afgedankte batterijen van e-bikes en e-scooters in zijn werkplaatsen in Amsterdam en Lyon. ‘In 2020 bleek dat we 74 procent van de batterijen die bij ons binnenkwamen konden repareren, waarna ze opnieuw gebruikt konden worden’, zegt medeoprichter Jan Bartels. ‘Uit de overige 26 procent konden we nog individuele cellen verwijderen, die dan gebruikt kunnen worden in andere toepassingen.’ Nowos onderhandelt ook met de makers van dit type batterijen om ze geschikter te maken voor reparatie en hergebruik.
Hergebruik
Bij iedere oplaadcyclus van een lithium-ionbatterij gaat een klein deel van de capaciteit verloren. Volgens de geruchtenmolen gaan de nieuwste generaties batterijen echter veel langer mee dan men aanvankelijk durfde te hopen. En dat blijkt te kloppen. Tesla stelt dat de batterijen van zijn nieuwste Modellen S en X na 320.000 kilometer een capaciteitsverlies laten zien van minder dan 20 procent.
Een onafhankelijk onderzoeker toonde aan dat batterijen van Tesla’s die tussen 2013 en 2020 werden geleverd gemiddeld jaarlijks niet meer dan 1 procent van hun actieradius verloren. En het kan nog beter: zowel Ford als het Chinese bedrijf CATL pakken dit jaar uit met de million mile battery, een lithium-ionbatterij waarmee een elektrische auto maar liefst 1,6 miljoen kilometer kan rijden.
Hoe dan ook is iedere lithium-ionbatterij na tien of vijftien jaar zo’n 20 tot 30 procent van zijn capaciteit kwijt. Zo’n batterij is niet meer geschikt om nog comfortabel te rijden, en de fabrikant is volgens de Europese regels verplicht het ding terug te nemen. Gelukkig zijn er toepassingen die zo’n gedeeltelijk opgebruikte batterij een tweede of misschien zelfs een derde leven kunnen geven.
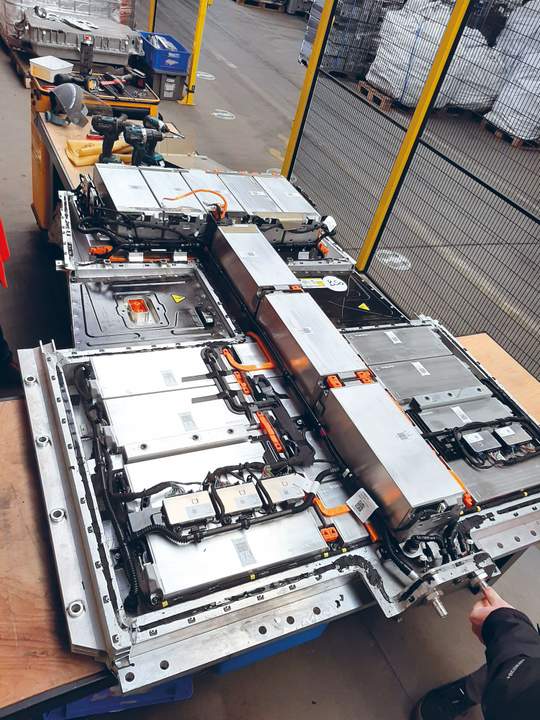
Zo kan men de beste modules gebruiken voor de aandrijving van golfkarretjes, vorkheftrucks en kleine schepen. In de fabrieken van Nissan rijden elektrische robotwagentjes rond die aangedreven worden door drie modules uit lithium-ionbatterijen die hun eerste leven doorbrachten in de elektrische Nissan Leaf. Volgens Nissan kunnen deze batterijen in hun nieuwe toepassing nog wel tien jaar mee.
De belangrijkste toepassing zit echter in de opslag van elektriciteit. In 2020 kregen Engie en Umicore de Febeliec Energy Award voor een Second Life-opslagsysteem van 1,2 megawatt (MW) in Olen. Het levert energie aan het net wanneer de vraag groot is en laadt zichzelf weer op door in de daluren stroom van het net te halen. Het systeem is gemaakt door de afgedankte lithium-ionbatterijen van 48 Renault Kangoo’s in containers met elkaar te verbinden tot één grote batterij. De behoefte aan dergelijke opslagsystemen zal toenemen nu we steeds meer gebruikmaken van zonne- en windenergie, bronnen die fluctueren met het weer.
Zowel in België als in Nederland zijn er bedrijven opgericht die afgedankte batterijen ombouwen voor een tweede leven in de energieopslag. De Johan Cruyff Arena in Amsterdam beschikt al sinds 2018 over een opslagsysteem van 3 MW dat is opgebouwd uit 148 nieuwe en afgedankte lithium-ionbatterijen van Nissan Leafs. Het systeem kan elektriciteit opslaan die tijdens daluren wordt geleverd door het net of de elektriciteit die wordt opgewekt door de 4.200 zonnepanelen op het dak van het stadion.
In België komen veel afgedankte batterijen van elektrische auto’s via het beheersorganisme Febelauto, dat verantwoordelijk is voor de controle, terecht bij Out of Use. De modules die nog bruikbaar zijn, krijgen via het bedrijf Watt4Ever een tweede leven in de energieopslag. Om branden en ontploffingen te voorkomen, worden de batterijen in speciale containers vervoerd en halen gespecialiseerde technici de spanning eraf. Modules en andere onderdelen die niet meer geschikt zijn voor hergebruik gaan naar recyclaging-installaties, zoals die van Umicore in Hoboken.
Recycling
Wanneer hergebruik niet langer een optie is, wordt recycling het eindstation in het leven van een lithium-ionbatterij. De batterijen bevatten tientallen kilo’s kostbare grondstoffen zoals lithium, nikkel, kobalt, mangaan, aluminium, koper, grafiet en zeldzame aardmetalen. Er wordt wereldwijd veel onderzoek gedaan naar de ontwikkeling van nieuwe methoden om zoveel mogelijk van die materialen te herwinnen.
Het Belgische bedrijf Umicore begon al in 2011 te pionieren met het recyclen van lithium-ion en nikkelmetaalhydride batterijen in een piloot-installatie in Hoboken. Die kan jaarlijks met een gepatenteerd pyrometallurgisch proces 7.000 ton herlaadbare batterijen verwerken. Dat komt overeen met 250 miljoen batterijen uit mobieltjes of 35.000 lithium-ionbatterijen uit elektrische auto’s. ‘We zijn vroeg begonnen omdat we klaar willen zijn op het moment dat de boom in elektrische auto’s begint’, zegt woordvoerster Marjolein Scheers. ‘In de eerste jaren gingen er vooral draagbare batterijen in, en ook productie-afval van bedrijven die batterijen voor elektrische auto’s maken.’ Scheers verwacht dat het aandeel van batterijen uit elektrische auto’s snel zal groeien.
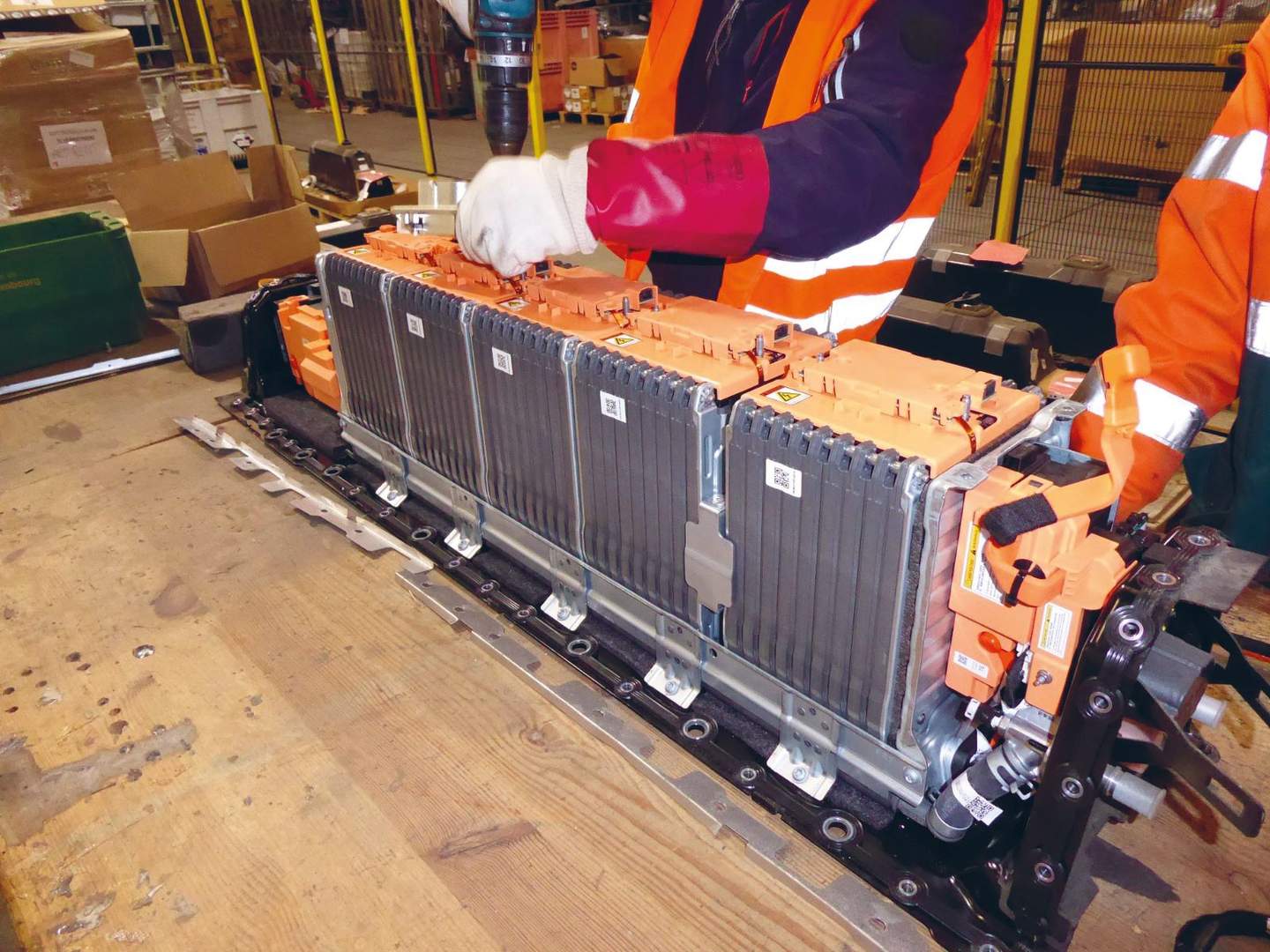
In Hoboken worden batterijen bij een hoge temperatuur gesmolten in een smelter. Daarbij ontstaat een legering van nikkel, kobalt en koper, materialen die via een hydro-proces van elkaar worden gescheiden. Scheers zegt dat het Umicore lukt om 95 procent van deze materialen terug te winnen. De overige materialen, zoals lithium, mangaan en zeldzame aardmetalen blijven achter in slakken. Er zijn gespecialiseerde bedrijven die uit deze slakken ook het lithium en de zeldzame aardmaterialen kunnen recupereren.
In 2030 zal wereldwijd zo’n 820.000 ton aan lithium-ionbatterijen gerecycled moeten worden. Scheers zegt dat Umicore tegen die tijd zijn capaciteit voor het recyclen van lithium-ionbatterijen zeker zal hebben opgeschaald. Ze voegt eraan toe dat het proces van Umicore bijzonder schoon is. De stroom die nog in de batterijen is opgeslagen, wordt gebruikt om het proces aan te sturen. Het proces veroorzaakt naar verluidt ook geen emissies die de omgeving belasten.
Uiteraard zit de concurrentie niet stil. Het Duitse bedrijf Duesenfeld heeft een pilootinstallatie gebouwd die jaarlijks 3.000 ton lithium-ionbatterijen uit elektrische auto’s kan verwerken. Batterijen van elektrische auto’s worden hier niet gesmolten, maar in een vacuüm-shredder versnipperd. Door verhitting laat men dan de vloeibare elektrolyt uit deze massa verdampen. Met behulp van magneten en filters haalt Duesenfeld vervolgens aluminium, koper en plastics uit het granulaat. Daarna worden met zuurbaden de overige materialen teruggewonnen in de vorm van lithiumcarbonaat, lithiumhydroxide en de sulfaten van mangaan, nikkel en kobalt. Volgens Duesenfeld kost deze methode minder energie dan de pyrometallurgische methode. Bovendien claimt Duesenfeld dat het erin slaagt om 91 procent van alle grondstoffen terug te winnen.
Naast gespecialiseerde spelers zijn er ook fabrikanten van lithium-ionbatterijen die de recycling zelf op zich willen nemen. Tesla is al begonnen met het recyclen van afgedankte batterijen in zijn gigafabriek in Nevada, en Volkswagen bouwt een recyclinginstallatie waarmee het meer dan 90 procent van alle grondstoffen zou terugwinnen.
Regelgeving
Reparatie en hergebruik van lithium-ionbatterijen is niet alleen zinvol vanuit het perspectief van het milieu, het zijn ook markten waarop bedrijven zonder al te veel problemen winst kunnen maken. Dat kan niet gezegd worden van recycling. Het is meestal goedkoper om nieuwe grondstoffen te gebruiken dan grondstoffen die via dure processen zijn teruggewonnen uit afgedankte batterijen. Bovendien bestaat er een trend in de industrie om het aandeel van de duurste grondstoffen – met name kobalt – steeds verder terug te dringen. Op zich is dat natuurlijk prima, maar kobalt is nu net de grondstof die het recyclen van een batterij lucratief kan maken.
Waar financiële prikkels zwak zijn of ontbreken, zal regelgeving de rol van motivator moeten overnemen. Europese regels schrijven nu al voor dat 95 procent van een afgedankte auto moet worden hergebruikt. Dat geldt ook voor elektrische auto’s, waarin de lithium-ionbatterij verreweg de zwaarste en meest kostbare component is. De EU heeft daarnaast ook plannen om vanaf 2030 quota in te voeren voor de minimale hoeveelheid gerecyclede grondstoffen in nieuwe lithium-ionbatterijen. Het doel is dat 20 procent van het kobalt, 10 procent van het lithium en 12 procent van het nikkel in nieuwe batterijen tegen 2035 afkomstig is uit afgedankte batterijen.
Hand in hand
Op YouTube toont een fraai filmpje hoe robots van het Duitse bedrijf ElringKlinger lithium-ionbatterijen produceren zonder dat er ook maar één mens aan te pas komt. Helaas is het een stuk lastiger om zo’n batterij na gebruik net zo effectief weer uit elkaar te halen. Het is bijvoorbeeld een probleem dat de componenten van een batterij aan elkaar zijn gelast. Volgens Carlton Cummins, oprichter van het Britse recyclingbedrijf Aceleron, moeten producenten en recyclers samen op zoek naar manieren om batterijen makkelijker demonteerbaar te maken. Dat gaat wellicht het snelst wanneer de producent zelf optreedt als recycler, zoals bij Tesla en Volkswagen.