Abonnementsmodellen voor intelligente machines kunnen bijdragen aan een circulaire economie.
De verbinding tussen geïntegreerde productiesystemen en dynamische bedrijfs- en technologische processen maakt het mogelijk producten winstgevender te fabriceren, de zogenaamde “slimme productie”. Maar als zelfs oude machines intelligent worden gekoppeld kan nog veel meer worden bereikt: het kan grondstoffen sparen, overproductie verhinderen, storingen voorkomen en de onderhoudsintervallen aanzienlijk verlengen. Dit zou de eerste stap kunnen zijn in de richting van een industriële circulaire economie, zoals aangetoond in het EU-project RECLAIM.
Beelden: Een rondleiding op de demosite van het Reclaim-project in een Gorenje-fabriek. Gorenje wil nieuwe en innovatieve manieren vinden om de time-to-market van een reeks producten te verkorten en de kwaliteit te verhogen. De digitalisering van de apparatuur en het vernieuwingsproces in de witte emaille-lijn zullen van cruciaal belang zijn om dit te bereiken.
We weten allemaal dat ons huidige economische systeem, dat grotendeels gebaseerd is op grondstoffenverbruik, onze planeet vernietigt en vervuilt. De Earth Overshoot Day (EOD) is dit jaar op 28 juli. Dat is de berekende datum waarop het grondstoffenverbruik van de mensheid dit jaar groter is dan de regeneratiecapaciteit van de aarde. Als wij en toekomstige generaties in welvaart willen blijven leven, is er maar één oplossing: niet meer grondstoffen verbruiken dan er terug kunnen groeien. We moeten zuinig omgaan met onze grondstoffen en ze consequent hergebruiken. Kortom, we hebben een circulaire economie nodig.
Begrippen zoals reparatie en hergebruik klinken redelijk - ze zouden ons in staat stellen om de bruikbare levensduur van producten in het systeem te verlengen. Zo'n economische verschuiving zou echter niets minder zijn dan een productierevolutie. Op sommige gebieden zijn er natuurlijk al veelbelovende benaderingen, maar met name de industriële productie produceert nog steeds enorme hoeveelheden afval. Productie verbruikt een enorm groot gedeelte van alle op de wereld beschikbare energie en drinkwater. En tegelijkertijd wordt in productieprocessen het leeuwendeel van de kooldioxide en andere broeikasgassen uitgestoten.
Onderzoekers uit de hele wereld bieden deze uitdagingen het hoofd, zowel op technisch, economisch en sociaal gebied. Sommigen zijn van mening dat de productie in de toekomst sterk verbonden moet worden om deze uitdagingen aan te pakken. Industrie 4.0, Smart Factory, kunstmatige intelligentie, horen we keer op keer. Maar zover zijn we nog lang niet. Er zijn baanbrekende bedrijven, maar de overgrote meerderheid van de fabrieken gebruikt conventionele machines die vaak al tientallen jaren in gebruik zijn. En ze leveren nog steeds betrouwbaar en nauwkeurig werk, maar in een traditionele, grondstoffen-verslindende omgeving.
Hergebruik en renovatie van oude machines
Als we grondstoffen willen besparen, energie-efficiëntie willen verhogen en dus duurzamer willen worden, moeten alle productieapparatuur en processtappen naadloos met elkaar verbonden en gesynchroniseerd zijn.
En dat is een probleem: ‘De meeste machines kunnen niet zomaar met sensoren worden uitgerust en in een gedigitaliseerde omgeving worden gebruikt’, legt Dr. Michael Peschl, hoofd van Onderzoek en Ontwikkeling bij Harms & Wende, uit. Het in Hamburg gevestigde bedrijf is een industriële leverancier van geautomatiseerde en handmatige lastechnologie en leidt het RECLAIM-project.
RECLAIM staat voor RE-manufaCturing and Refurbishment of LArge Industrial equipMent. Dit door de EU gefinancierde project wil strategieën en technologieën demonstreren die het hergebruik van industriële apparatuur in oude, gerenoveerde en nieuwe fabrieken mogelijk maken. Onderzoekers en vertegenwoordigers van de industrie, uit negen Europese landen, hebben RECLAIM opgericht met het ambitieuze doel reproduceerbare oplossingen aan te reiken die de Europese productiesector kunnen helpen om aan deze en toekomstige eisen te voldoen.
‘Harms & Wende heeft twee belangrijke doelstellingen met het RECLAIM-project’, zegt Michael Peschl. ‘Ten eerste, hoever kunnen we eigenlijk gaan met hergebruik en renovatie, modernisatie en vernieuwing? Waar liggen de grenzen?’ Er zijn nieuwe benaderingen voor hergebruik en renovatie nodig om ervoor te zorgen dat de Europese industrie concurrerend blijft en het milieu wordt beschermd, aldus de onderzoeker. Verschillende bedrijven hebben in het kader van RECLAIM met succes bestaande machines achteraf uitgerust met slimme sensoren. Het is de bedoeling om ze te integreren in het controle- en regelnetwerk van hun fabrieken, zowel volledig als gedeeltelijk geautomatiseerd. ‘Ten tweede willen we weten hoe machines in de toekomst moeten worden ontworpen om te voldoen aan de eisen van een circulaire economie’, voegt hij eraan toe.
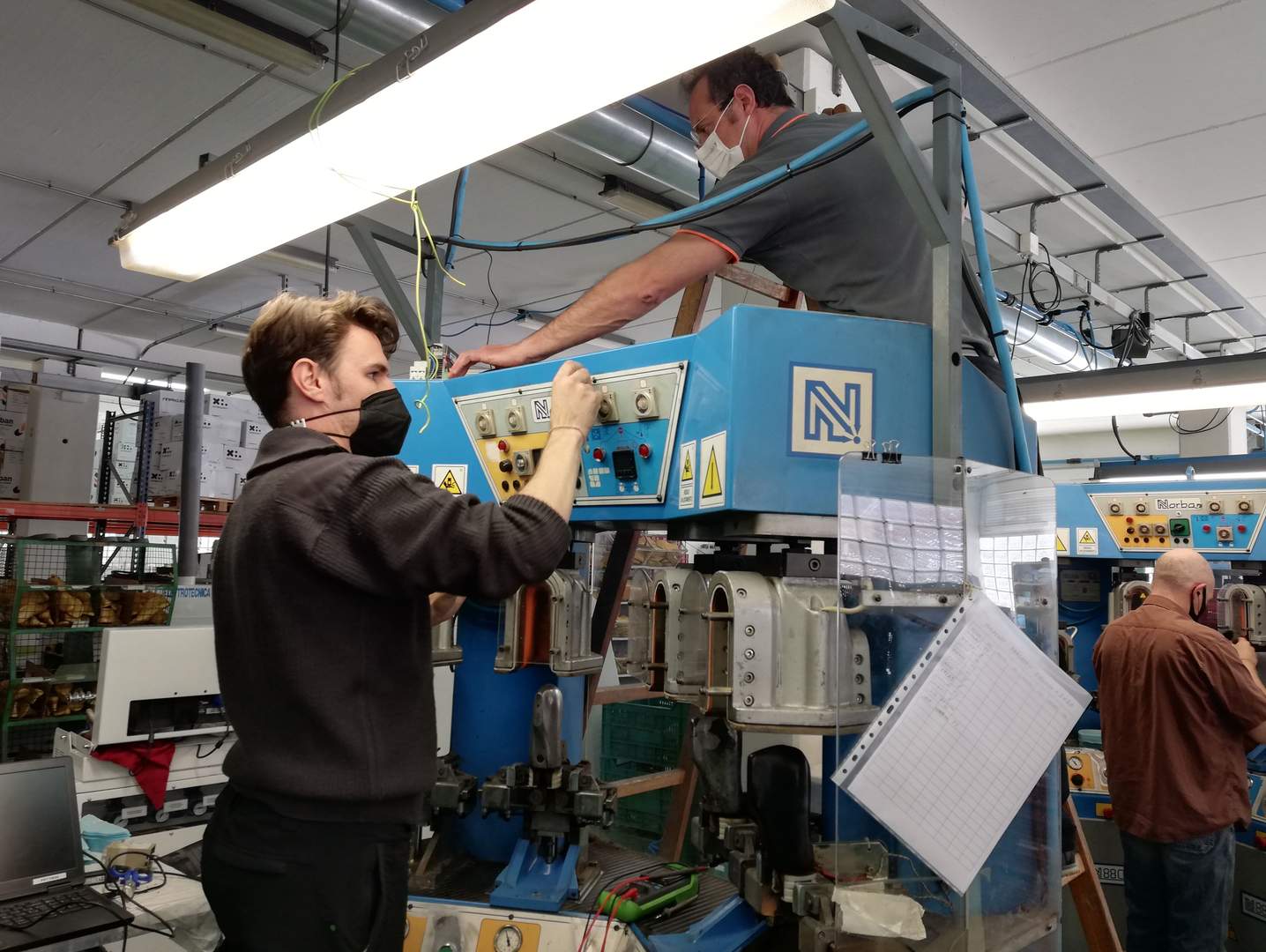
Dit is niet alleen een technische of mechanische kwestie. Het gaat er niet alleen om materialen te scheiden en ze volledig te recycleren, ook al is dat nog steeds belangrijk om te doen. Het punt is: hoe minder grondstoffen een economie nodig heeft, hoe gemakkelijker het zal zijn om over te stappen van grondstof-intensieve productie- en consumptiemodellen naar een duurzame, CO2 arme en afvalvrije economie.
Peschl en zijn RECLAIM-collega's willen de behoefte aan grondstoffen zo veel mogelijk beperken. Daarom zoeken ze bijvoorbeeld naar manieren om onderhoudsintervallen zoveel mogelijk uit te stellen. Ze ontwikkelen flexibele machineconcepten die op grotere schaal kunnen worden gebruikt, en overwegen of het niet verstandiger is om machines te huren in plaats van ze te kopen.
Daarvoor hebben ze data nodig, de zogenaamde big data: over machines, productie, materialen, machineoperators en de hele productieomgeving. Daarnaast hebben ze details nodig over planning, de toepassingsgebieden van producten, het gedrag van eindgebruikers, enzovoort. En ze kunnen al die informatie niet verwerken zonder kunstmatige intelligentie.
Industrie 4.0 Audit
Om het digitaliseringspotentieel van productiefaciliteiten te bepalen, hebben Maurice Herben, programmadirecteur voor het Fraunhofer Project Center aan de Universiteit van Twente en zijn collega's van het Fraunhofer Instituut voor Productietechnologie IPT de Industrie 4.0 Audit ontwikkeld. Deze uitgebreide audit belooft bedrijven een inzichtelijk overzichtsperspectief te bieden op hun huidige digitaliseringsstatus, evenals een op onderzoek gebaseerde, data-gestuurde blauwdruk voor toekomstig succes.
De audit begint met een Quick Scan ter plaatse om inzicht te krijgen in de specifieke behoeften, doelstellingen en verwachte uitdagingen van het bedrijf om een op maat gemaakte auditaanpak te kunnen bepalen. Het omvat gesprekken ter plaatse met de leiders en medewerkers van het bedrijf. Met de informatie van de Quick Scan zullen de Fraunhofer-experts een passend auditplan ontwikkelen.
De Industrie 4.0 Audit neemt maximaal twee weken in beslag, met interne workshops met diverse stakeholders. Het omvat een analyse van de huidige toestand, een benchmark- en gap-analyse en ten slotte de ontwikkeling van een stappenplan. Het bedrijf ontvangt een gedetailleerd verslag en een op maat gemaakt actieplan van Maurice Herben en zijn medewerkers. Indien gewenst bieden zij ook implementatieondersteuning en workshops.
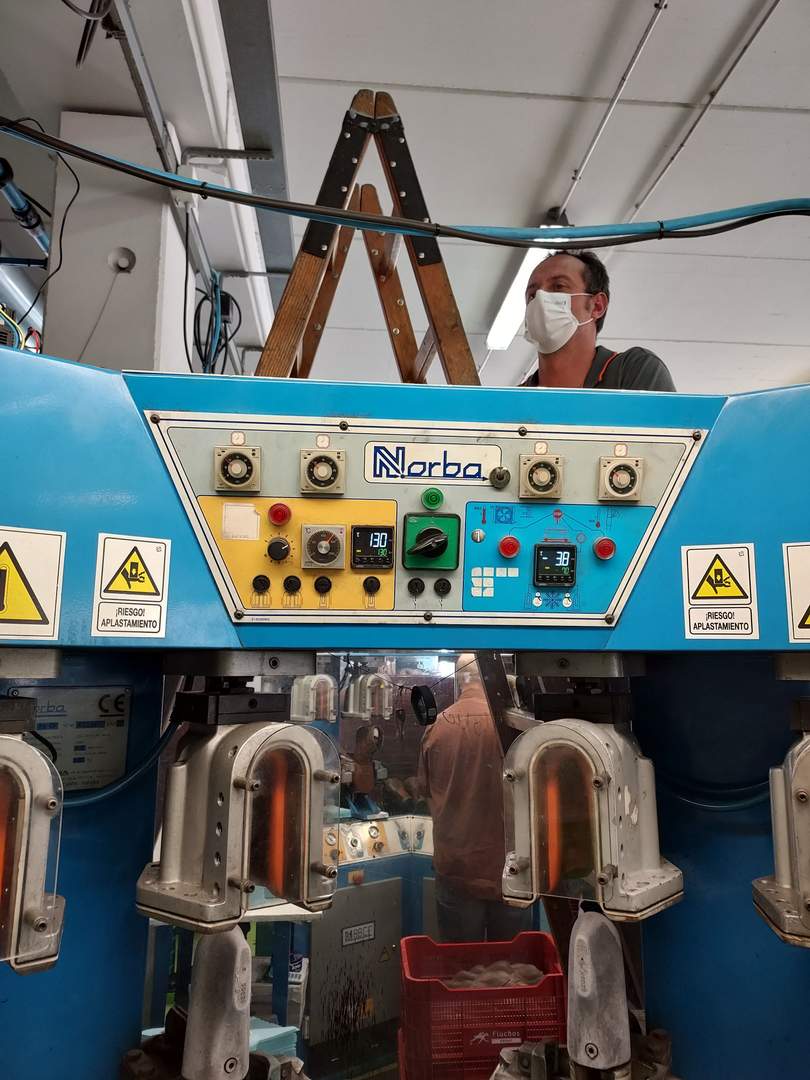
‘Het belangrijkste voordeel van onze audit voor de klant is dat veel bedrijven niet eens weten wat er allemaal mogelijk is met digitale transformatie’, zegt Herben. ‘Voor de afzonderlijke gebieden hebben we verschillende experts die bekend zijn met de nieuwste trends en technologische ontwikkelingen in de slimme industrie, zoals adaptieve productie of analytics in productie, Digital Twin of abonnementsmodellen. Zij kennen de specifieke voordelen, kansen en uitdagingen.’
Onlangs heeft de Nederlandse Smart Industry Hub “Innovatiecluster Drachten” (ICD) de 4.0 Audit toegepast om een actieplan te ontwikkelen om een volledig papierloze productie in te voeren. ‘Het klinkt eigenlijk als veel minder werk dan het in werkelijkheid is’, herinnert Herben zich. De ICD-bedrijven Quadient, Variass, Ventura Systems, NTS Norma en Photonis 's hebben twee jaar succesvol gewerkt aan oplossingen voor papierloze productie. De resultaten gaan verder dan instructies voor het bedienen van machines op iPads. De nieuwe totaaloplossing vraagt om een innovatieve IT-infrastructuur die, gekoppeld aan het productieproces, kan inspelen op de nieuwste consumentenbehoeften.
Machine as a Service (MaaS)
Volgens het Fraunhofer Project Center maken analyses in productie en Digital Twins nieuwe bedrijfsmodellen mogelijk – met een bredere scope of een consistente duurzame oriëntatie. Dit vraagt natuurlijk om een transformatie van de huidige productieprocessen. Als bedrijven bovendien bereid zouden zijn om niet alleen hun productie maar ook hun financieringsprincipes te herzien, zouden abonnementsmodellen de volgende grote stap kunnen zijn: bedrijven zoals MAN, Siemens, Philipps, Caterpillar en Saint Gobain hebben het abonnementsmodel in plaats van het aanschafmodel al geïmplementeerd. Steeds meer bedrijven willen gewoon machines en gereedschap gebruiken; toegang tot een dergelijke dienst is belangrijker dan de aanschaf. Voor veel bedrijven is dit een kwestie van beschikbaarheid, flexibiliteit, keuzemogelijkheden en duurzaamheid.
De toenemende digitalisering van processen en producten wekt bij productiebedrijven grote verwachtingen wat betreft de daaruit voortvloeiende potentiële waardevermeerdering. De toenemende digitalisering biedt mogelijkheden voor een nieuwe interpretatie van industriële abonnementsmodellen. Traditionele distributiemodellen hebben tot aanzienlijke overproductie en verspilling geleid - met de bijbehorende kosten voor fabrikanten en klanten. Abonnementen zouden dit kunnen voorkomen. Abonnementsmodellen presteren beter en zorgen ervoor dat de belangen van de fabrikant en de klant op elkaar zijn afgestemd. Bovendien genieten machinegebruikers ook voordelen, zoals: een verbeterde dynamiek in productiviteit en kwaliteit, uitgebreide onderhouds- en reparatieservices, kostentransparantie en lagere gebruikskosten, evenals een vereenvoudigde heraanbesteding.
‘Abonnementsmodellen zijn op het moment nog niet ingeburgerd’, verklaart Michael Peschl. ‘Maar de voordelen zijn duidelijk. We moeten vertrouwen en acceptatie creëren. Dat is nu ook precies wat we met RECLAIM beginnen te doen.’ Nu vragen Peschl en zijn collega's aangepaste Europese fiscale afschrijvingsmogelijkheden om abonnementsbenaderingen te ondersteunen die de circulaire economie bevorderen.
Het RECLAIM-project heeft met succes gebruik gemaakt van het idee van renovatie en herfabricage op basis van big data-analyses, machine learning, voorspellende analyses en optimalisatiemodellen waarbij gebruik wordt gemaakt van deep learning-technieken en Digital Twin modellen. Steakholders waren hierdoor in staat om weloverwogen beslissingen te nemen over de vraag of zware machines die het einde van hun levenscyclus naderen, moeten worden geherfabriceerd, gemoderniseerd of gerepareerd.
‘Harms & Wende heeft de lastechniek binnen het RECLAIM-project aanzienlijk kunnen verbeteren’, zegt Peschl voordat hij met gepaste trots de resultaten presenteert. ‘Tot nu toe hebben we het aantal incidenten met 50% verminderd, de onderhoudskosten ook met 50% verlaagd en de levensduur van onze systemen met acht jaar verlengd.’ Zodra de RECLAIM-projectpartners de opgedane kennis en de fundamentele bevindingen over de ontwerpvereisten van de circulaire economie implementeren, zijn verdere verbeteringen in de zeer nabije toekomst heel waarschijnlijk.