Hoe genereer je op grote schaal hernieuwbare waterstof? Hoe maak je koolwaterstoffen uit gerecycleerde CO2? Vlaamse onderzoeksinstellingen werken aan technologische oplossingen om de klimaatopwarming een halt toe te roepen.
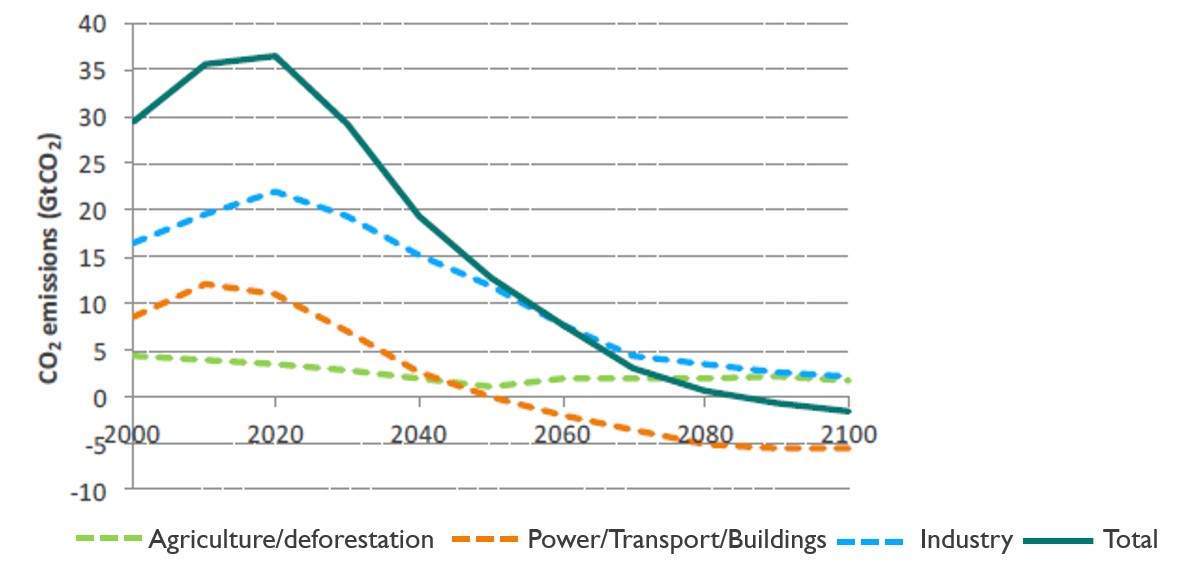
Als we de klimaatopwarming willen beperken tot twee graden Celsius, dan moet de netto wereldwijde CO2-emissie naar nul dalen tegen 2050. Met de hulp van onder meer zonnepanelen en wagens die rijden op groene stroom kan de CO2-uitstoot snel dalen in de transport- en bouwsector, maar in andere industriële sectoren zoals de landbouw of de staal-en cementindustrie is zo’n snelle reductie veel minder realistisch. Het IPCC (The Intergovernmental Panel on Climate Change) gaat ervan uit dat de uitstoot in die sectoren niet helemaal zal verdwijnen en dat die enkel kan gecompenseerd worden door de actieve verwijdering van CO2 uit de lucht.
Er is veel aandacht voor de ontwikkeling van technieken om CO2 uit de lucht op te vangen en op te slaan. Bart Onsia, expert energieomzetting en business development manager bij imec/EnergyVille onderzoekt evenwel al de volgende stap: hoe kunnen we deze opgevangen CO2 hergebruiken? “Om CO2 te kunnen hergebruiken, moet je het eerst omzetten in componenten die op een of andere manier van nut zijn”, vertelt hij. “Een boom gebruikt zonlicht om water en CO2 uit de lucht om te zetten in koolwaterstoffen. In essentie is dat hetgeen wij ook willen doen, maar dan efficiënter.”
De verschillende nieuwe technologieën die daarvoor onderzocht worden, vallen samen onder de noemer ‘Power-to-Molecules’. Het idee erachter is steeds hetzelfde: water en CO2 omzetten in waardevolle stoffen voor de industrie. Afhankelijk van de stof die dat oplevert, wordt soms ook over ‘Power-to-Gas’ of ‘Power-to-Liquids’ gesproken. "De moleculen in ‘Power-to-Molecules’ kunnen zowel op een gas of een vloeistof slaan”, zegt Bart Onsia. “Het kan gaan om brandstoffen zoals waterstof, methanol of ethanol, maar evengoed om verbindingen zoals ethyleen of syngas die als basiscomponenten kunnen gebruikt worden voor de chemische industrie, om er bijvoorbeeld polymeren van te maken.”
Voor die omzetting is energie nodig, liefst hernieuwbare energie. Net zoals planten kunnen we daarvoor beroep doen op zonne-energie (in dat geval soms ‘solar fuels’ genoemd), maar ook windenergie komt in aanmerking. De zon schijnt niet elke dag even fel en het waait niet altijd even hard, waardoor het energie-aanbod fluctueert. Op momenten dat er veel hernieuwbare energie wordt opgewekt, kan de overtollige elektriciteit omgezet worden in chemische energie. Idealiter gebeurt dat ter plaatse. “Met energietransport gaan verliezen gepaard. Daarom zouden offshore-windparken hun opgewekte energie liever rechtstreeks kunnen omzetten in de vorm van waterstof”, illustreert Bart Onsia. “Zie het als een nieuwe vorm van batterij-opslag: In plaats van de overproductie op te slaan in een batterij, slaan we ze op als hernieuwbare brandstof”.
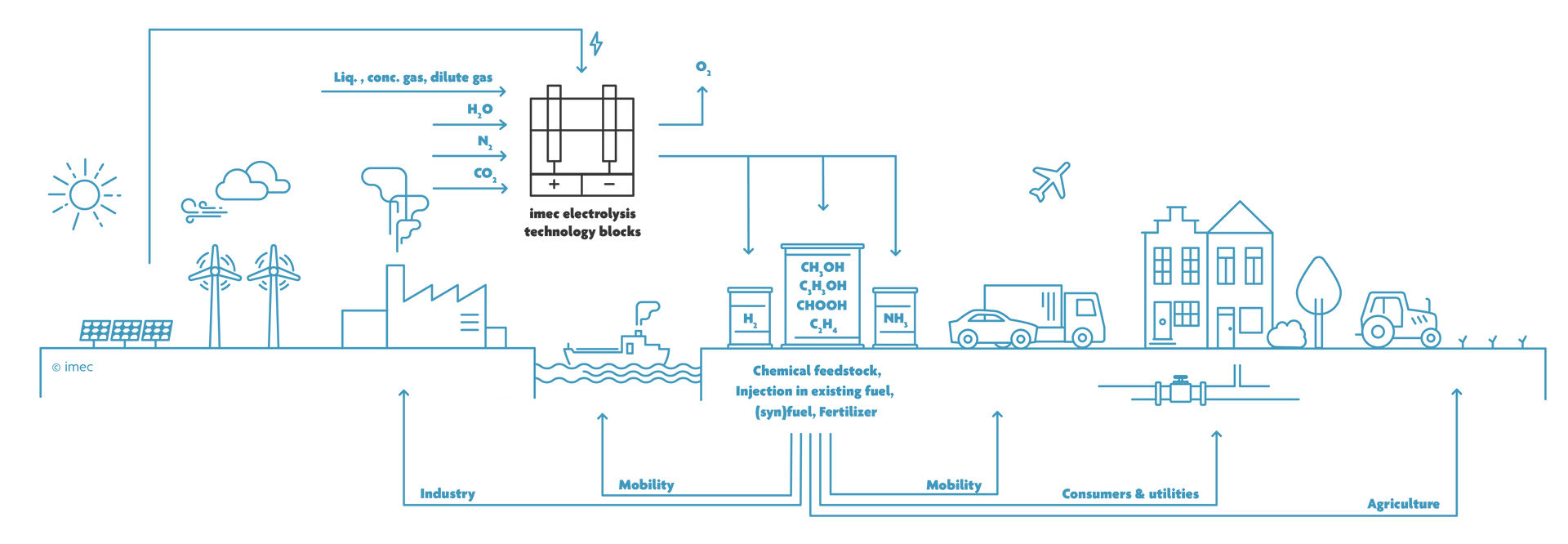
Van grijze waterstof naar groene waterstof
Als we waardevolle moleculen willen produceren op basis van hernieuwbare energie, dan is waterstof (H2) de meest voor de hand liggende molecule. In de chemische industrie en de staalindustrie wordt nu voornamelijk beroep gedaan op ‘grijze’ waterstof, geproduceerd door stoomreforming. Bij dit proces worden aardgas en stoom op hoge temperatuur samengevoegd en ontstaat niet alleen waterstof, maar ook CO2.
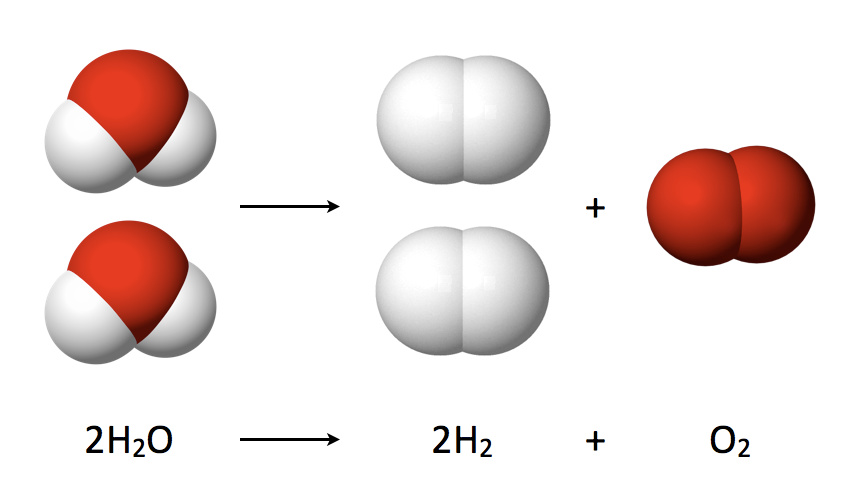
Nochtans bestaat er een meer ecologisch verantwoorde manier om waterstof te produceren: door elektrolyse van water. Wie zich de chemieproefjes uit de middelbare school herinnert, weet wat er gebeurt wanneer je twee metalen plaatjes (elektrodes) onderdompelt in water en aansluit op een spanningsbron: er ontstaan bubbeltjes. Onder invloed van elektrische stroom ontstaat waterstofgas bij de negatieve pool en zuurstofgas bij de positieve.
Toch verwarmen we onze huizen nog niet met waterstof en rijden er amper waterstofauto’s op de baan. Elektrolysetoestellen voor industriële toepassingen zijn dan wel al enige tijd op de markt, ze zijn momenteel niet kostenefficiënt genoeg om er op grote schaal groene waterstof mee te oogsten. Voor slechts vijf procent van de wereldwijde waterstofproductie wordt beroep gedaan op elektrolyse. “Met stoomreforming betaal je ongeveer twee euro per kilogram waterstof. Met elektrolyse ligt die kost momenteel minstens drie keer hoger, afhankelijk van de schaal”, verklaart Bart Onsia. “Dat heeft niet alleen te maken met de efficiëntie van het proces, maar ook met de kosten van de stroom, de distributiekosten en het gebrek aan schaalvoordeel. Ik ben ervan overtuigd dat we elektrolysetoestellen veel kleiner en efficiënter kunnen maken, waardoor de kosten voor groene waterstofproductie zullen dalen, zodat ze concurrentieel wordt met de manier waarop waterstof nu wordt geproduceerd.”
Hoe kunnen we dit proces efficiënter maken en welke technologische innovaties hebben we daarvoor nodig? Er bestaan verschillende manieren om een elektrolysetoestel te bouwen, maar de zogenaamde alkaline-elektrolyse staat momenteel het verst in de ontwikkeling. Op basis van 5 MW (pakweg de capaciteit van één windmolen in de Noordzee die op volle toeren draait), kan dergelijk toestel honderd kilogram waterstof per uur leveren. Laat ons eerst eens kijken hoe deze technologie er vandaag in de praktijk uitziet.
Het cilindervormige toestel is opgebouwd uit 170 elektrolysecellen, die in serie geschakeld worden. Iedere cel bestaat uit twee ringvormige elektrodes waarvan de diameter zo’n twee meter kan bedragen. Tussen de elektrodes is telkens een separator-membraan geplaatst. Deze separator laat ionen door, maar voorkomt dat gassen vermengd geraken: het geproduceerde waterstofgas en zuurstofgas mogen niet in elkaars buurt komen, want dat zou een explosief mengsel opleveren. Het geproduceerde gas moet ook zo snel mogelijk weggeleid worden, want het mag het water niet wegduwen van de elektroden. De cruciale reactie in een elektrolysetoestel speelt zich dus af aan het oppervlak van de elektrodes, waar drie verschillende aggregatietoestanden – vast, vloeibaar en gasvormig - met elkaar in contact komen.
De oppervlakte van een voetbalveld in een colablikje
Aangezien de efficiëntie bepaald wordt door chemische reacties die aan een oppervlak plaatsvinden, beschik je maar beter over een zo groot mogelijk oppervlak. Imec heeft samen met de KU Leuven een zogenaamd ‘nanomesh’ ontwikkeld, een robuust materiaal met een ontzettend grote oppervlakte per volume-eenheid. Philippe Vereecken, wetenschappelijk directeur energie-omzetting bij imec, legt uit wat we ons daarbij moeten voorstellen: “Vergelijk twee emmers, de ene gevuld met tennisballen, de andere met zandkorrels. In de emmer met zandkorrels zal een grotere oppervlakte per volume-eenheid aanwezig zijn. Bij ons nieuwe materiaal is deze effectieve oppervlakte nóg veel groter gemaakt: voor elke micrometer dikte zal het beschikbare oppervlak 33 keer groter worden. Wanneer we een frisdrankblikje volledig met dit nanomesh zouden opvullen, dan zou dat blikje de oppervlakte van een voetbalveld bevatten en toch nog steeds voor drie kwart uit lucht bestaan.”
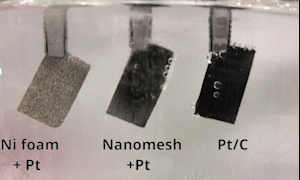
Een grote oppervlakte alleen volstaat niet, het materiaaloppervlak moet ook snel reactanten kunnen opnemen en reactieproducten kunnen afvoeren. Het materiaal moet dus tegelijk over een poreuze structuur beschikken. Het nanomesh, dat er onder de microscoop uitziet als een driedimensionaal kippengaas, combineert beide eigenschappen. “Het materiaal is opgebouwd uit miljoenen rechtopstaande nanodraadjes die ook horizontaal met elkaar verbonden zijn”, zegt Vereecken. “Dankzij deze regelmatige structuur combineert het nanomesh een hoge porositeit met een ongeziene oppervlakte per volume-eenheid en kunnen de afmetingen ervan zowat volledig naar behoefte aangepast worden.”
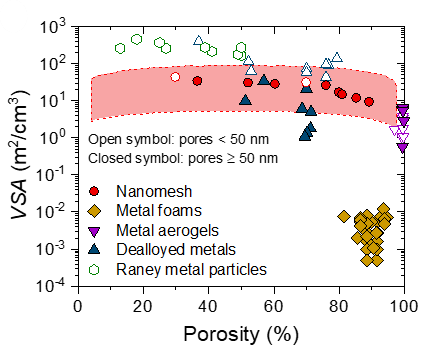
Door de oppervlaktevergroting kunnen de elektrodes veel dunner gemaakt worden. Tegelijk werkt imec ook aan dunnere membranen om de afstand tussen de elektrodes nog verder te reduceren. Het voordeel daarvan is dat de verliesstromen kleiner worden. “Hoe meer stroom je door een elektrolysecel stuurt, hoe meer waterstof er gevormd wordt, maar ook hoe sneller de verliezen gaan oplopen. Dat laatste kunnen we vermijden door alles te miniaturiseren met deze nanomesh -en membraantechnologie”, legt Philippe Vereecken uit. Tot slot kan de efficiëntie nog verder opgedreven worden door betere coatings te maken voor de elektroden. “Daarbij worden zeer dunne laagjes van specifieke materialen afgezet. Ook dat is iets wat we binnen imec uitstekend beheersen, omdat we alle dunne-film-depositie-technologie in huis hebben”, klinkt het. Innovatie in de nano-elektronica zal dus de grootschalige productie van groene waterstof helpen mogelijk maken. Dat zal stap voor stap gebeuren, benadrukt Bart Onsia. “In eerste instantie gebruiken we vloeibaar water, maar gaandeweg zullen we evolueren naar elektrolysecellen die waterdamp kunnen omzetten in waterstof en uiteindelijk zelfs naar cellen die het vocht meteen uit de lucht halen.”
Met een drietrapsraket naar een koolstofneutrale samenleving
Deze elektrolysetechnologie zal een sleutelrol spelen in de transitie naar een koolstofarme economie, en wel op twee manieren. Op lange termijn zal ze ons helpen om broeikasgassen om te zetten en te hergebruiken, maar op kortere termijn kan groene waterstof de koolstofemissies in verschillende sectoren helpen reduceren. Uit de energie die in de waterstofmoleculen zit verankerd kan elektriciteit, warmte of beweging gegenereerd worden. Een brandstofcel werkt volgens het omgekeerde principe van elektrolyse: het genereert elektriciteit door waterstof en zuurstof uit de lucht om te zetten in water. De waterstofauto is de bekendste toepassing, maar waterstof kan ook ingezet worden voor zwaar industrieel vervoer, zoals schepen en vrachtwagens. Daarnaast vormt waterstof ook de ultieme duurzame brandstof, omdat er geen CO2 vrijkomt tijdens de verbranding.
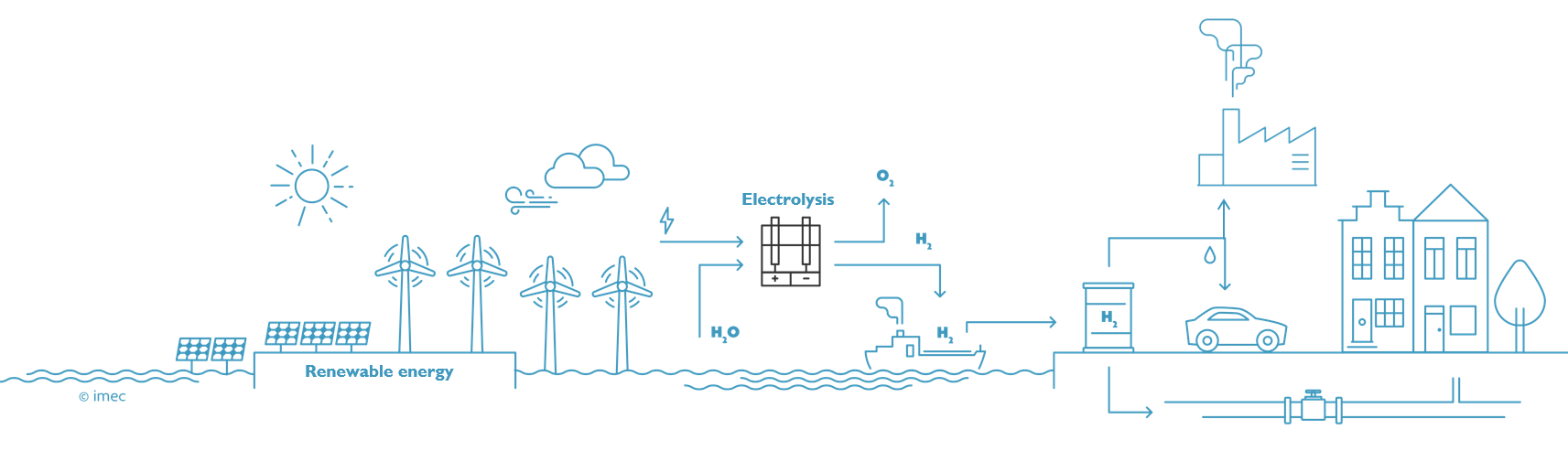
Bart Onsia ziet vooral in de staal-en de cementindustrie een direct nut voor de introductie van groene waterstof. “De bevolking groeit, er wordt continu gebouwd, dus zal er een blijvende vraag zijn naar beton en staal. De staalindustrie zal volgens de voorspellingen van het IPCC met dertig procent blijven groeien tot 2050. Voor elke 2,3 ton staal die gemaakt wordt op basis van steenkool, komt 1 ton CO2 vrij. In plaats van ijzererts zouden we ook waterstof kunnen gebruiken, maar dan hebben we wel gigantische hoeveelheden nodig, zo’n 50 miljoen ton waterstof per jaar. In de cementindustrie zitten we met een dubbel probleem, want CO2 komt er niet alleen vrij als verbrandingsproduct. Bij de productie van 1 ton cement uit calciumcarbonaat ontstaat 0.9 ton CO2, de ene helft uit de reactie en de andere helft uit de warmte die daarvoor nodig is. Ook daar zie ik dus nog veel marge voor decarbonisatie.”
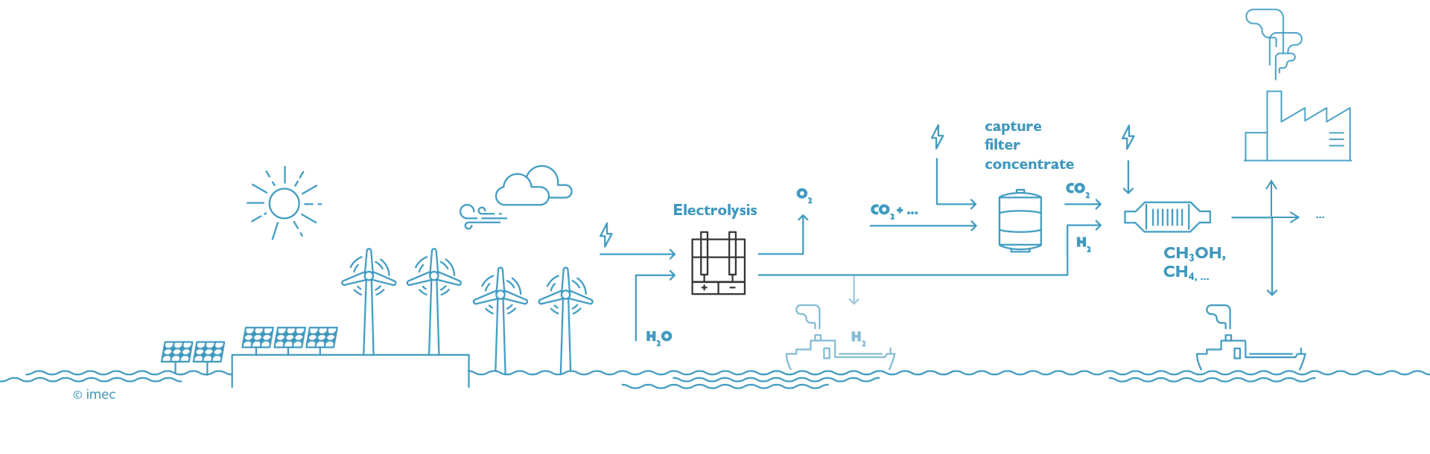
De grootschalige productie van groene waterstof zal nodig zijn om af te kicken van onze verslaving aan fossiele brandstoffen, maar dat vormt slechts de eerste stap. In een volgende fase zal die hernieuwbare waterstof gebruikt worden om in combinatie met CO2 rechtstreeks methanol, methaan of andere producten te maken. “Uit waterstof en CO2 kan je waardevolle stoffen maken voor de chemische industrie. Vandaag gebeurt dat in verschillende stappen, waarbij elke stap een bepaald rendement heeft. Wij beschikken over de technologie om alles in één stap te doen: een directe en selectieve omzetting van CO2 naar stoffen zoals methanol, ethanol of mierenzuur”, zegt Bart Onsia.

Aanvankelijk zal nog pure, opgeconcentreerde CO2 gebruikt worden, maar in een latere fase zal de CO2 rechtstreeks uit de fabrieksschoorstenen worden opgevangen, om uiteindelijk CO2 uit de lucht te gebruiken (met een CO2-concentratie van 400 deeltjes per miljoen). Op die manier wordt een circulaire CO2-economie mogelijk. Een andere langetermijndoestelling van het ‘Power-to-Molecules’-programma is om stikstof uit de lucht meteen om te zetten in stoffen die nuttig zijn voor de landbouw. Dergelijke methodes zullen nodig zijn om tegen 2050 koolstofneutraal te worden. Om deze duurzame energietechnologie snel te kunnen invoeren en opschalen, is een doorgedreven innovatie cruciaal.