3D-print je tandarts binnenkort een tandprothese op maat terwijl jij in de wachtzaal zit? Mijn doctoraatsonderzoek bewijst dat het mogelijk is om keramieken tandprotheses te 3D-printen die sterk genoeg zijn om kauwkrachten te overleven.
Beeld: Het 3D-printen van een tandprothese.
Additive manufacturing of 3D-printen is vandaag niet meer weg te denken in de samenleving. Je kent waarschijnlijk wel iemand die thuis een 3D-printer heeft om zelf gadgets of onderdelen te bouwen. 3D-printers worden ondertussen ook gebruikt voor medische toepassingen, in de lucht- en ruimtevaart en voor de auto-industrie. Prototypes, gepersonaliseerde voorwerpen en patiënt-specifieke implantaten zijn slechts enkele van de toepassingen van 3D-printen. Het laat toe om te bezuinigen op materiaal, sneller te werken en uitzonderlijk complexe designs te bouwen die onmogelijk waren met de bestaande technologieën. Alhoewel het 3D-printen van polymeren en metalen reeds industrieel wordt toegepast, staat de ontwikkeling van het 3D-printen van keramiek nog in de kinderschoenen. Maar wat is keramiek eigenlijk?
Typische voorbeelden van keramiek bij je thuis zijn klei of porselein, je kopje waar je koffie uit drinkt of het bord waar je van eet. Heb je je al eens afgevraagd hoe deze gemaakt worden? Misschien heb je al eens een cursus pottenbakken gevolgd. Dan geef je het materiaal de juiste vorm op de draaitafel of met de hand, je bakt je ontwerp in de oven en je kan het gebruiken. Hetzelfde proces wordt toegepast voor technische keramiek; ze krijgt de juiste vorm, wordt gebakken op temperaturen tot 2000°C en daarna is ze klaar voor gebruik. Keramiek is gekend om haar “humeurige gedrag”, waar het kleinste foutje in het materiaal de prestatie van het volledige voorwerp bepaalt: een ketting is maar zo sterk als haar zwakste schakel. Het vermijden van materiaal- of printdefecten bij 3D-printen is één van de meest onderzochte factoren.
Er zijn zeven 3D-printcategorieën met elk hun eigen subtechnologieën. Voor keramische materialen worden vooral technologieën gebruikt waarbij een mengsel van een bindmateriaal en keramisch poeder wordt geprint. Na het printen wordt het bindmateriaal verwijderd door een chemisch of thermisch proces, en daarna wordt de keramische poedercomponent afgebakken om het finale design te verkrijgen.
Van goud naar keramiek
Wereldwijd lijden 3,9 miljard mensen aan één of andere vorm van tandproblemen, twee procent van de bevolking lijdt aan ernstig tandverlies. De mondgezondheid heeft bovendien een grote invloed op jouw levenskwaliteit. Gezonde tanden zijn niet alleen essentieel om ervoor te zorgen dat jij vlot en gezond kan eten, ze hebben ook een substantiële invloed op ons fysiek uiterlijk. Om al die redenen gebruikten de oude Egyptenaren al tandprotheses. Zij hadden eenvoudige houten exemplaren, die later vervangen werden door ivoor en zelfs getrokken dieren- of mensentanden. Als je een oude tandprothese hebt, is dat misschien nog een metalen of gouden tandprothese. Vandaag gebruiken we keramische tandprotheses. Bezorgdheid over toxiciteit en de zoektocht naar meer een natuurlijke look zorgde ervoor dat de tandheelkunde evolueerde van metalen naar keramische tandrestauraties.
Als je recent een tandprothese hebt gekregen, is die waarschijnlijk uit zirkoniakeramiek gemaakt. Vandaag de dag is ongeveer zestig procent van de tandprotheses gemaakt van dat materiaal. Zirkonia is een veelzijdig materiaal. Op zichzelf is het niet stabiel bij kamertemperatuur, dus we voegen er peper en zout aan toe, bekend als metaaloxides. Afhankelijk van de hoeveelheid peper en zout variëren de eigenschappen van zirkoniakeramiek. Tijdens mijn doctoraat gebruikte ik 3 mol% yttriumoxide als peper en zout. Dit geeft de zirkoniatanden hun uitstekende sterkte en een zeer natuurlijke, witte look. Dit type zirkonia wordt ook wel “keramisch staal” genoemd, omdat het de enige niet brosse oftewel taaie keramiek is. Wanneer je jouw koffietas thuis laat vallen, zal die barsten en in stukken uiteen vallen. Je koffietas is dus zeer bros. Je wilt niet dat jouw tandprothese het meteen begeeft tijdens het kauwen van je eten. Wanneer je zirkoniatandprothese zal beginnen scheuren, zal het lokaal op microscopische schaal een beetje uitzetten en die scheur terug dichtduwen, waardoor jij niet meteen terug naar de tandarts moet elke keer als je noten gegeten hebt.
De huidige productie van zirkoniatandprotheses bestaat uit computerondersteund ontwerpen en vervaardigen (CAD/CAM) frezen van (voor)gesinterde zirkoniablokken. Tot negentig procent van het materiaal wordt verspild en de gebruikte boren en frezen slijten zeer snel. Het potentieel om tanden zo mooi mogelijk op maat te maken is beperkt zonder achteraf nog een gekleurde laag aan te brengen. Frezen introduceert ook onvermijdelijk bewerkingsfouten, zoals scheuren, krassen en zelfs veranderingen in de eigenschappen van het materiaal.
Kunnen we zirkoniatanden 3D-printen?
Mijn doctoraat richtte zich op het produceren van zirkoniakeramieken tandprotheses met behulp van twee verschillende 3D-printtechnieken, meer specifiek digital light processing en inkt jetting. Ik heb in vier jaar vele tanden en stalen geprint, en die daarna telkens terug gebroken om naar het materiaal te kijken onder de microscoop en de mechanische eigenschappen te meten. Het doel van mijn doctoraat was om te bepalen of deze 3D-printtechnieken kunnen worden gebruikt om tandprotheses te maken die minstens even goed zijn als degene die vandaag al worden geplaatst.
Techniek 1: digital light processing
De digitale light processor printer maakte gebruik van een UV LED-licht om een UV-reactieve keramische pasta laag per laag uit te harden. Na het printen van de tandprothese, wordt deze nog gebakken in een oven om het poeder aan elkaar te laten smelten en de finale vorm te krijgen. Van alle onderzochte printparameters bleek het verminderen van de geprinte laagdikte tot 15 μm de prestatie van de zirkoniaprints het meeste te helpen. Zo’n fijne laagdikte maakt het mogelijk om complexe designs zoals tandprotheses of implantaten te 3D-printen met nauwkeurige afmetingen en specifieke details. In vergelijking met zirkoniakeramiek gemaakt volgens de klassieke processen, waren de ge-3D-printe materialen minder sterk. Kleine foutjes in het materiaal, zoals scheuren of luchtbellen zorgen voor een lagere sterkte. Ze bezaten wel de minimale sterkte nodig om als een dentale restauratie gebruikt te worden.
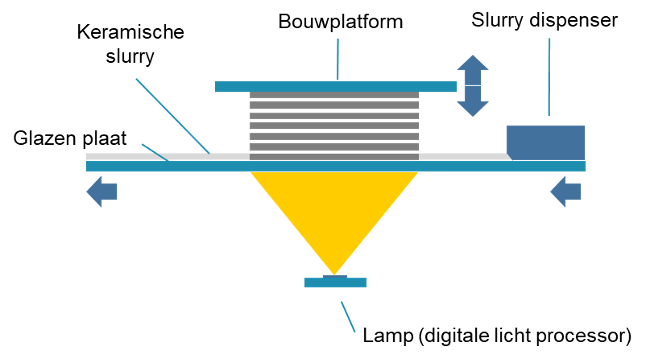
Een dunne laag UV-uithardbare, keramische pasta wordt uitgespreid over een glazen plaat bij digitaal licht processen. Het 3D object wordt gebouwd op een omgekeerd bouwplatform door het laag per laag uitharden van de pasta tegen het op en neer bewegend bouwplatform.
Techniek 2: inkt jetting
Deze technologie werkt zoals jouw printer thuis. Inktdruppels gemaakt van een zeer vloeibare slurrypasta met daarin keramische deeltjes en een bindmiddel worden druppelsgewijs op een bouwplatform gestort. Het verschil met je printer thuis, is dat we hier duizenden lagen inktdruppels op elkaar bouwen om een 3D voorwerp te maken. De dikte van één geprinte keramieken pasta laag was slechts 10,5 μm. Na het printen moeten we opnieuw de tandprotheses in de oven bakken om alle binder te verwijderen, en de poederdeeltjes aan elkaar te laten smelten. Door de zeer fijne laagdikte, waren deze tandprotheses nog accurater. De sterkte van deze tandprotheses was iets hoger dan die gemaakt via digitaal light processen. De sterktes waren bijna vergelijkbaar met sterktes van zirkonia gemaakt via de klassieke processen.
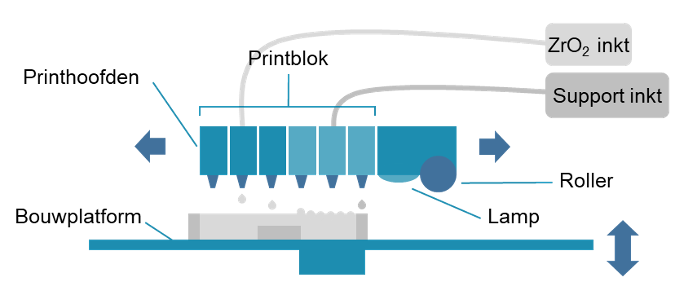
Inkt jetten werkt als een letterlijke 3D-printer, waarbij kleine inktdruppeltjes laag per laag neerslagen op een bouwplatform. De lamp verhit de druppeltjes zodat elke laag kan uitharden.
Hoe presteren tanden gemaakt in een 3D-printer?
In het begin testte ik enkel simpele balkjes of schijfjes om het gedrag van de geprinte zirkoniakeramiek te meten. Maar natuurlijk willen we testen of tandprotheses zelf ook kunnen geprint worden en of ze in deze vorm ook het gewenste gedrag vertonen. Na maanden van enkel simpele vormpjes te printen, heb ik me kunnen uitleven door een heel resem tanden en andere leuke gadgets te printen. Het is mogelijk om de meest complexe kerstmisdecoraties te printen, maar gelukkig ook tandprotheses. De geprinte tandprotheses waren volledig dens en weken niet af van de gewenste vorm. Helaas was net zoals bij de simpele vormpjes, de sterkte van de ge-3D-printe tandprotheses lager dan die van de tandprotheses die vandaag gebruikt worden. Alle ge-3D-printe tandprotheses waren evenwel sterk genoeg om voldoende bijtkrachten te weerstaan en in aanmerking te komen voor klinische toepassing.
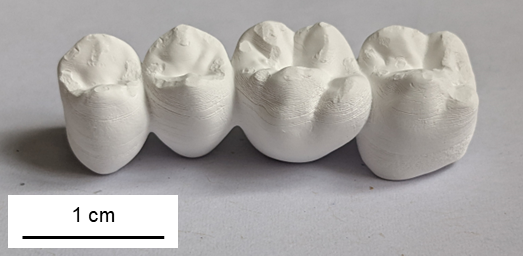
Beide onderzochte 3D-printtechnieken lieten toe om dense zirkoniatandprotheses met nauwkeurige afmetingen te produceren die sterk genoeg zijn voor klinische toepassing. Dit onderzoek vormde een goede aanzet voor het 3D-printen van keramische tandprotheses en de resultaten zijn ook veelbelovend voor andere industrieën. Dankzij 3D-printen zullen er nieuwe, meer complexe designs kunnen gemaakt worden. Niet enkel tandprotheses, maar ook de zirkoniaimplantaten waarop de tandprothese geplaatst wordt, kunnen ge-3D-print worden. We kunnen de hechting van deze implantaten verbeteren door een poreuze buitenste laag te printen, waardoor je eigen bot er kan ingroeien en deze implantaten dus steviger vast zitten. Beide 3D-printtechnologieën laten ook toe om verschillende materialen te combineren in één design, waardoor de mechanische prestatie en esthetiek van de dentale bruggen kan verbeterd worden. Je eigen tanden hebben een kleurgradiënt, waarbij ze wat geler zijn dichter tegen je tandvlees, en wat lichter en doorschijnender aan de andere kant. Via 3D-printen kunnen we deze kleurvariatie meteen maken in één proces. Het gebruik van verschillende materialen kan ook leiden tot een betere prestatie en een meer duurzame tandprothese. Er is nog veel werk, want de ge-3D-printe tandprotheses zijn nog niet zo goed als de klassieke tandprotheses vandaag. Verbeteringen in de compositie van de keramische pasta die geprint wordt, een betere hechting van de lagen tijdens het 3D-printen en het minimaliseren van foutjes die mee in het materiaal geprint worden, zijn eerste zaken die aangepast moeten worden om de geprinte materialen even goed te maken. Verder onderzoek over de lange-termijnprestaties van de ge-3D-printe tandprotheses is ook nodig voordat deze klinisch kunnen gebruikt worden. Indien deze aanpassingen succesvol zijn, kan jij binnen enkele jaren een meer duurzame ge-3D-printe tandprothese volledig afgewerkt naar jouw wensen laten plaatsen bij de tandarts.
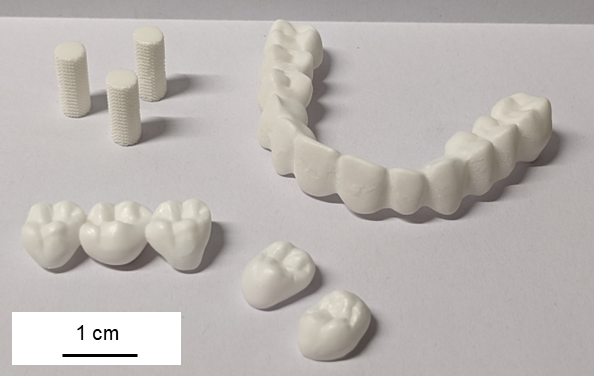